Film containing alginate membrane layer and manufacturing method thereof
A technology of alginate, manufacturing method, applied in the direction of skin care preparations, chemical instruments and methods, membranes, etc.
- Summary
- Abstract
- Description
- Claims
- Application Information
AI Technical Summary
Problems solved by technology
Method used
Image
Examples
Embodiment 1
[0040] A non-woven fabric made of polypropylene (PP) is used as a liquid-absorbable thin-layer carrier 10 to absorb about 4% (weight percent) of calcium lactate as the salt compound aqueous solution 22, and then coated with about A 2% (weight percent) sodium alginate solution is used as the salt compound aqueous solution 22, with a thickness of 1.1 mm. After cross-linking, an alginate film layer 20 with a thickness of about 1 mm can be formed on the polypropylene (PP) non-woven fabric. , That is, a layer of hydrocolloid complex film with a network structure. When the non-woven fabric made of polypropylene (PP) has a rough surface non-woven fabric as the cross-linking contact surface, the formed alginate film layer 20 will be combined with the non-woven fabric, that is, the thin layer carrier 10 ; And if the non-woven fabric made of polypropylene (PP) uses a smooth non-woven fabric as the cross-linked contact surface, the formed alginate film layer 20 can be separated from the n...
Embodiment 2
[0042] A non-woven fabric (non-woven fabric) made of polypropylene (PP) and nylon (Nylon) with a thickness of 0.42mm is used as a thin layer carrier 10 that can absorb liquid, and 2% (weight percentage) sodium alginate is immersed in a continuous immersion method Solution: After scraping off the excess solution on the surface 11 of the non-woven fabric (ie thin layer carrier 10), spray 4% (weight percent) calcium lactate solution on the upper and lower surfaces (11) to continuously produce a cloth-containing thickness of about 0.72 mm film 1 containing alginate film layer 20. If it is desired to obtain a thicker alginate film layer 20, after the calcium lactate solution has been applied, in the order of sodium alginate and calcium lactate, one or both sides of the finished film 1 are sprayed and delivered. In order to achieve the required thickness of the film 1.
Embodiment 3
[0044] A non-woven fabric (non-woven fabric) made of polypropylene (PP) and nylon (Nylon) with a thickness of 0.42mm is used as the liquid-absorbable thin-layer carrier 10, and 4% (weight percent) calcium lactate is immersed in a continuous immersion method Solution: After scraping off the excess solution on the surface 11 of the non-woven fabric (ie thin layer carrier 10), spray 2% (weight percent) sodium alginate solution on the upper and lower surfaces (11) to continuously produce a cloth-containing thickness of about A film 1 containing an alginate film layer 20 of 0.72 mm. If it is desired to obtain a thicker alginate film layer 20, after the sodium alginate solution has been used, calcium lactate and sodium alginate are sequentially sprayed on one or both sides of the finished film 1 The cross-linking effect can reach the required thickness of the film 1.
[0045] In addition, when the film containing the alginate film layer of the present invention is actually manufacture...
PUM
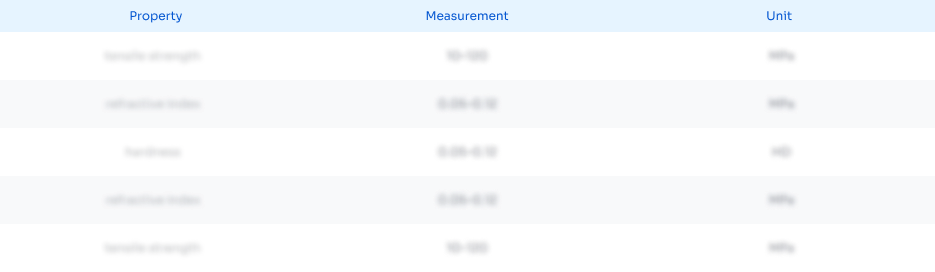
Abstract
Description
Claims
Application Information

- Generate Ideas
- Intellectual Property
- Life Sciences
- Materials
- Tech Scout
- Unparalleled Data Quality
- Higher Quality Content
- 60% Fewer Hallucinations
Browse by: Latest US Patents, China's latest patents, Technical Efficacy Thesaurus, Application Domain, Technology Topic, Popular Technical Reports.
© 2025 PatSnap. All rights reserved.Legal|Privacy policy|Modern Slavery Act Transparency Statement|Sitemap|About US| Contact US: help@patsnap.com