Optimal control method for strip tail shear by flying shear at continuous annealing unit inlet
A continuous annealing unit, optimized control technology, applied to rolling mill control devices, metal rolling, manufacturing tools, etc., can solve problems such as complex control, and achieve the effect of reducing downtime
- Summary
- Abstract
- Description
- Claims
- Application Information
AI Technical Summary
Problems solved by technology
Method used
Image
Examples
Embodiment Construction
[0015] The present invention proposes an optimal control method for the shearing of the inlet flying shear and the tail of the continuous retreating unit, including:
[0016] Maintain the unit to convey the belt steel at a constant speed VL;
[0017] When performing belt-tail shearing, the flying shears are controlled to decelerate from the shearing speed Vcut with an acceleration A for a uniform deceleration time T, then run at a low speed and a constant speed for a time Tcon after deceleration, and then accelerate from the low speed with an acceleration A for a uniform time T to Vcut, so that The shear amount of the belt tail is increased by ΔL, so that the last piece of scrap steel strip at the belt tail falls into the scrap conveying system through the flying shears;
[0018] Where Tcon is determined according to ΔL, and the time T is calculated as follows:
[0019] T = - AT CON ...
PUM
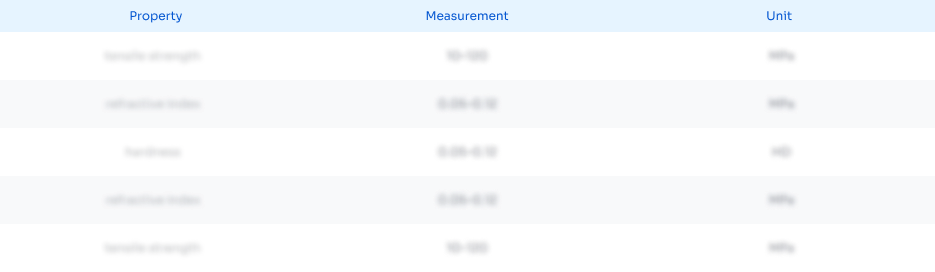
Abstract
Description
Claims
Application Information

- R&D
- Intellectual Property
- Life Sciences
- Materials
- Tech Scout
- Unparalleled Data Quality
- Higher Quality Content
- 60% Fewer Hallucinations
Browse by: Latest US Patents, China's latest patents, Technical Efficacy Thesaurus, Application Domain, Technology Topic, Popular Technical Reports.
© 2025 PatSnap. All rights reserved.Legal|Privacy policy|Modern Slavery Act Transparency Statement|Sitemap|About US| Contact US: help@patsnap.com