Continuous casting billet strengthening device and strengthening method in continuous casting process
A strengthening device and continuous casting slab technology, which is applied in the field of metallurgical continuous casting, can solve problems such as huge equipment, difficulty in popularization, and inappropriate control
- Summary
- Abstract
- Description
- Claims
- Application Information
AI Technical Summary
Problems solved by technology
Method used
Image
Examples
Embodiment 1
[0031] Embodiment 1: The continuous casting slab 2 with a certain thickness on the surface is formed after the molten steel passes through the vibrating crystallizer 1 . The shot blaster 3 after the fixed position can throw the steel shot 5 according to a certain speed range, and the steel shot 5 hits the surface of the continuous casting slab 2 through the shot blasting channel 7 . Protective cover 4 can be beneficial to the collection of steel shot 5 and safe production. The steel shot 5 enters the steel shot collection box 6 after being collected, and enters the shot blaster 3 through the shot pipeline 7 . The continuous casting slab 2 treated by the strengthening device of the continuous casting slab in the above continuous casting process can offset part of the thermal stress, reduce the number and length of cracks, and reduce the tendency of the slab to heat up and bulge, thereby improving the surface of the slab quality. The speed range of the thrown steel shot 5 can ...
Embodiment 2
[0032] Embodiment 2: Similar to the strengthening device of the continuous casting slab in the continuous casting process of the aforementioned embodiment 1, it is preferable to make the shot blaster 3 have a certain distance relative to the continuous casting slab 2, and the blasting device 3 can be determined according to the needs of the continuous casting process. The installation position of pill device 3. Wherein, the shot blaster 3 can be installed on one or more sides of the continuous casting slab 2; it can be installed symmetrically, asymmetrically, or independently. In addition, preferably the size of the outlet on the lower side of the protective cover 4 is set to 1.5-2 times the diameter of the steel shot, and other equipment that assists in collecting the steel shot can also be added. Preferably, the maximum diameter of the protective cover 4 is 1.2-1.5 times the diameter of the shot blasting channel, and there is a certain distance between the lower end of the p...
PUM
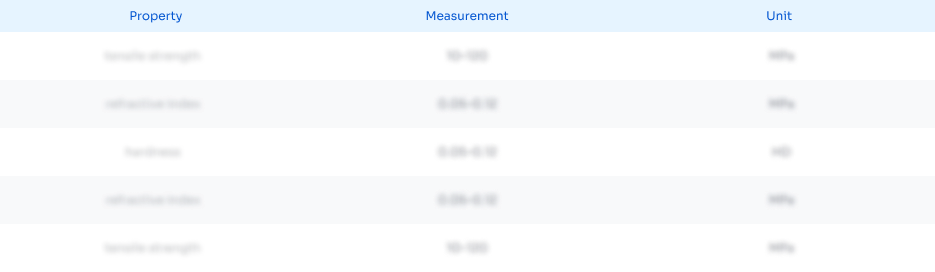
Abstract
Description
Claims
Application Information

- R&D
- Intellectual Property
- Life Sciences
- Materials
- Tech Scout
- Unparalleled Data Quality
- Higher Quality Content
- 60% Fewer Hallucinations
Browse by: Latest US Patents, China's latest patents, Technical Efficacy Thesaurus, Application Domain, Technology Topic, Popular Technical Reports.
© 2025 PatSnap. All rights reserved.Legal|Privacy policy|Modern Slavery Act Transparency Statement|Sitemap|About US| Contact US: help@patsnap.com