A high-efficiency forging method for healing internal hole-type defects of billets with large aspect ratio
A technology of internal holes and height-to-diameter ratio, which is applied in the field of forging, can solve the problems of inability to completely forge the internal hole defects and loose axes of billets with large height-to-diameter ratios, achieve good results, reduce scrap, and increase the internal strain of billets
- Summary
- Abstract
- Description
- Claims
- Application Information
AI Technical Summary
Problems solved by technology
Method used
Image
Examples
Embodiment 1
[0043] The blanks with large aspect ratio used in this example are 9 continuous casting blanks, the original size is Φ600mm×2000mm, the aspect ratio is 3.33, the material is S45C+B, and the blank with large aspect ratio weighs about 4.4 tons. The temperature is 1200°C. Due to the relatively large height and diameter of the continuous casting slab, the upsetting process cannot be used for it, and it can only be directly elongated. First use the wide anvil radial compaction method to press down, and after pressing into a flat square, return it to the furnace and heat it to 1200°C and keep it warm for 3 hours. Figure 5 This is the distribution diagram of the equivalent strain field of the blank when the wide anvil radial compaction method is used for 20% reduction obtained through finite element simulation. It can be seen from the figure that the strain of the wide anvil radial compaction is concentrated in the center of the blank, which can be up to 0.4 or more. And as figur...
Embodiment 2
[0047] The billet with large aspect ratio used in this example is a steel ingot, the original size is Φ1000mm×3000mm, the height-diameter ratio is 3, the material is No. 45 steel, the billet with large aspect ratio weighs about 18 tons, and the heating temperature of the billet is 1200°C . There are relatively serious shrinkage porosity in the center of the steel ingot. Due to the relatively large height and diameter of the steel ingot billet, the upsetting process cannot be used for it, and it can only be directly elongated. First use the wide anvil radial compaction method to press down, and after pressing into a flat square, return it to the furnace and heat it to 1200°C and keep it warm for 5 hours. After the heat preservation is over, turn the billet 90° and use the WHF method to draw it two times, and the reduction rate is 20% each time. After the two passes, continue to elongate the blank and round it to Φ600mm. After the forging is completed, flaw detection is carri...
PUM
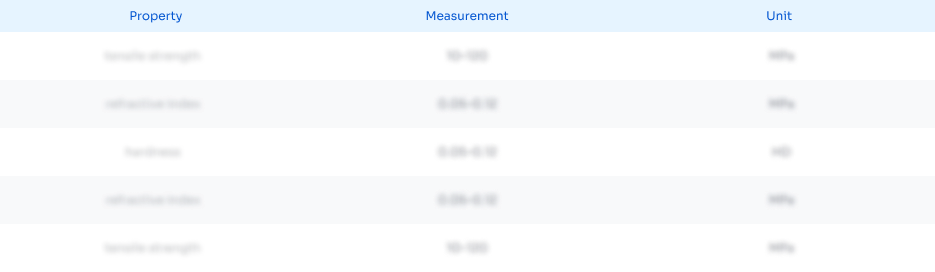
Abstract
Description
Claims
Application Information

- R&D
- Intellectual Property
- Life Sciences
- Materials
- Tech Scout
- Unparalleled Data Quality
- Higher Quality Content
- 60% Fewer Hallucinations
Browse by: Latest US Patents, China's latest patents, Technical Efficacy Thesaurus, Application Domain, Technology Topic, Popular Technical Reports.
© 2025 PatSnap. All rights reserved.Legal|Privacy policy|Modern Slavery Act Transparency Statement|Sitemap|About US| Contact US: help@patsnap.com