Automobile front damper installation plate blanking die
A front shock absorber and mounting plate technology, which is applied in the field of blanking molds for automobile front shock absorber mounting plates, can solve problems such as high processing costs, difficulty in picking parts, and easy formation of curling, etc., to improve product quality and processing efficiency , reduce production costs, and prevent workpiece deformation
- Summary
- Abstract
- Description
- Claims
- Application Information
AI Technical Summary
Problems solved by technology
Method used
Image
Examples
Embodiment Construction
[0019] figure 1 It is a schematic structural diagram of the present invention, as shown in the figure: The blanking die for the mounting plate of the automobile front shock absorber of the present invention includes an upper die body and a lower die body, and the upper die body is provided with corresponding parts for cutting the workpiece. The upper die cutting die 1 and the punch 2 of the side and punching hole 6 and the presser 3 for elastically compressing and positioning the workpiece; the lower die body is provided with the upper and lower die body opposite to the presser 3 for supporting the workpiece The lower die 4, which cooperates with the upper die cutting die 1 and the punch 2 to trim and punch the workpiece, is located on the periphery of the lower die 4 and is provided with upper and lower die cutting die 1 for pressing and trimming the workpiece. The blank holder 5 is elastically supported. The lower die 4 is vertically opposite to the punch 2 and is provided wi...
PUM
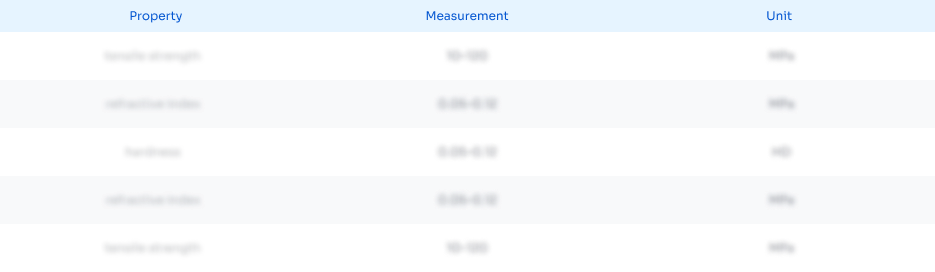
Abstract
Description
Claims
Application Information

- Generate Ideas
- Intellectual Property
- Life Sciences
- Materials
- Tech Scout
- Unparalleled Data Quality
- Higher Quality Content
- 60% Fewer Hallucinations
Browse by: Latest US Patents, China's latest patents, Technical Efficacy Thesaurus, Application Domain, Technology Topic, Popular Technical Reports.
© 2025 PatSnap. All rights reserved.Legal|Privacy policy|Modern Slavery Act Transparency Statement|Sitemap|About US| Contact US: help@patsnap.com