Ceramic filter pressing plate, manufacturing method thereof and filter press using same
A technology of filter press plate and filter press, which is applied in the field of filter press to achieve the effect of good surface gloss, wide source of raw materials and long service life
- Summary
- Abstract
- Description
- Claims
- Application Information
AI Technical Summary
Problems solved by technology
Method used
Image
Examples
Embodiment 1
[0044] The ceramic filter press plate of the present invention is formed by pressing the ceramic waste slag mixture, and the ceramic waste slag mixture includes the following components by weight percentage:
[0045] Ceramic waste 50%;
[0046] Polypropylene 50%.
[0047] Among them, the ceramic waste slag in the raw material comes from the waste water waste slag produced by the polishing or cutting process of ceramics. , turn waste into treasure, and reduce the consumption of polypropylene and other materials, which can reduce production costs. The filter plate made of ceramic waste residue also has high temperature resistance, corrosion resistance, high pressure resistance, good surface gloss, and long service life. long advantage.
Embodiment 2
[0049] The ceramic filter press plate of the present invention is formed by pressing the ceramic waste slag mixture, and the ceramic waste slag mixture includes the following components by weight percentage:
[0050] Ceramic waste 35%;
[0051] Polyethylene 65%.
Embodiment 3
[0053] The ceramic filter press plate of the present invention is formed by pressing the ceramic waste slag mixture, and the ceramic waste slag mixture includes the following components by weight percentage:
[0054] Ceramic waste 40%
[0055] Polypropylene 60%.
PUM
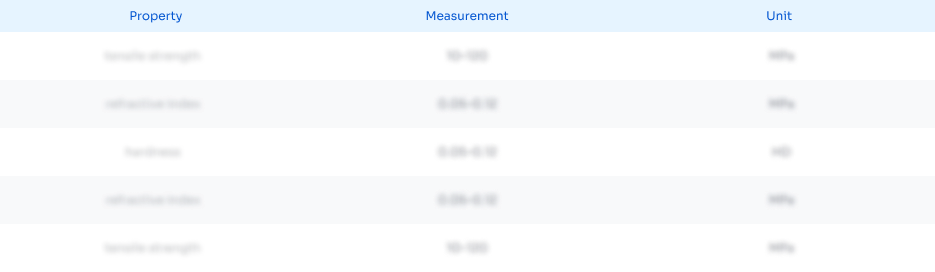
Abstract
Description
Claims
Application Information

- R&D
- Intellectual Property
- Life Sciences
- Materials
- Tech Scout
- Unparalleled Data Quality
- Higher Quality Content
- 60% Fewer Hallucinations
Browse by: Latest US Patents, China's latest patents, Technical Efficacy Thesaurus, Application Domain, Technology Topic, Popular Technical Reports.
© 2025 PatSnap. All rights reserved.Legal|Privacy policy|Modern Slavery Act Transparency Statement|Sitemap|About US| Contact US: help@patsnap.com