Quick joint for high-tension cables
A high-voltage wire, fast technology, applied in the direction of connection, conductive connection, electrical component connection, etc., can solve the problems of low safety, material waste, easy disconnection of joint parts, etc., to improve the wiring speed, reduce costs, and save time. Effect
- Summary
- Abstract
- Description
- Claims
- Application Information
AI Technical Summary
Problems solved by technology
Method used
Image
Examples
Embodiment 1
[0030] Both ends of the threading pipe 1 of the present invention are respectively provided with at least one threaded hole 2, the threaded hole 2 is provided with a screw 3, the threaded rod 3 is fixed by a nut 4, and the middle part of the threading pipe is provided with a baffle.
[0031] Installation process
[0032] The present invention only needs to insert the ends of two high-voltage wires 7 to be connected into the left and right threading pipes 1 respectively, so that the ends of the two high-voltage wires 7 are in contact with the baffles 6 in the threading pipe 1 respectively. Then use two screw rods 3 at one end of the threading pipe to rotate and compact the high-voltage line 7 downwards, and at the same time use the nut 4 on the screw rod 3 to self-lock the screw rod 3 to prevent the screw rod 3 from loosening due to swinging. Carry out the same steps at the other end to complete the connection of the high voltage line 7.
Embodiment 2
[0034] At least one boss 5 is provided at both ends of the threading pipe 1, and the middle part of the boss 5 is provided with a threaded hole. The threaded hole is connected with the threading pipe. The threaded hole is provided with a screw, which is fixed by a nut. 6.
[0035] Installation process
[0036] The present invention only needs to insert the ends of two high-voltage wires 7 to be connected into the left and right threading pipes 1 respectively, so that the ends of the two high-voltage wires 7 are in contact with the bottoms of the threading pipes 1 respectively. Then use two screw rods 3 at one end of the threading pipe 1 that are matched with the threaded holes 2 of the boss 5 to rotate downward to compact the high-voltage line 7, and at the same time use the nut 4 on the screw rod 3 to cooperate with the threaded holes 2 of the boss 5 to automatically carry out the screw rod 3 The lock prevents the loosening of the screw rod 3 due to swinging. Carry out the ...
Embodiment 3
[0038] Both ends of the threading pipe 1 of the present invention are respectively provided with at least one threaded hole 2, the threaded hole 2 is provided with a screw 3, the screw 3 is fixed by a nut 4, the threading pipe is placed at both ends of the high-voltage line 7, and the threading pipe and the high-voltage line 7 are crimped and casted .
[0039] Installation process
[0040] The present invention only needs to insert the ends of two high-voltage wires 7 to be connected into the left and right threading pipes 1 respectively, so that the ends of the two high-voltage wires 7 are in contact with the bottoms of the threading pipes 1 respectively. Then use two screw rods 3 at one end of the threading pipe 7 to rotate downwards and compact the high-voltage line 7, and simultaneously use the nut 4 on the screw rod 3 to self-lock the screw rod 3 to prevent the screw rod 3 from loosening due to swinging. Carry out the same steps at the other end to complete the connectio...
PUM
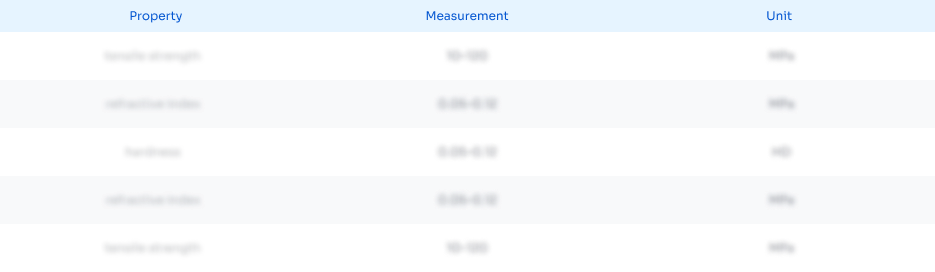
Abstract
Description
Claims
Application Information

- R&D Engineer
- R&D Manager
- IP Professional
- Industry Leading Data Capabilities
- Powerful AI technology
- Patent DNA Extraction
Browse by: Latest US Patents, China's latest patents, Technical Efficacy Thesaurus, Application Domain, Technology Topic, Popular Technical Reports.
© 2024 PatSnap. All rights reserved.Legal|Privacy policy|Modern Slavery Act Transparency Statement|Sitemap|About US| Contact US: help@patsnap.com