Molten gel back pressure control system and method for electrically controlled injection molding machine
A technology of control system and injection molding machine, which is applied in the field of melt adhesive back pressure control system, can solve the problems of low pressure control precision and inability to guarantee high precision of products, and achieve the effect of simple structure, dynamic response speed and easy parameters
- Summary
- Abstract
- Description
- Claims
- Application Information
AI Technical Summary
Problems solved by technology
Method used
Image
Examples
Embodiment Construction
[0022] In order to make the object, technical solution and advantages of the present invention clearer, the present invention will be further described in detail below in conjunction with the accompanying drawings and embodiments. It should be understood that the specific embodiments described here are only used to explain the present invention, not to limit the present invention.
[0023] Such as figure 1 and 2 As shown, the melt adhesive back pressure control system of the electronically controlled injection molding machine of the present invention is mainly used for dynamic and real-time control of the melt adhesive back pressure of the electronically controlled injection molding machine. It can be understood that the melt adhesive back pressure control system 2 can be a part of the electronically controlled injection molding machine, or the melt adhesive back pressure control system 2 can be used as a device independent of the electronically controlled injection molding m...
PUM
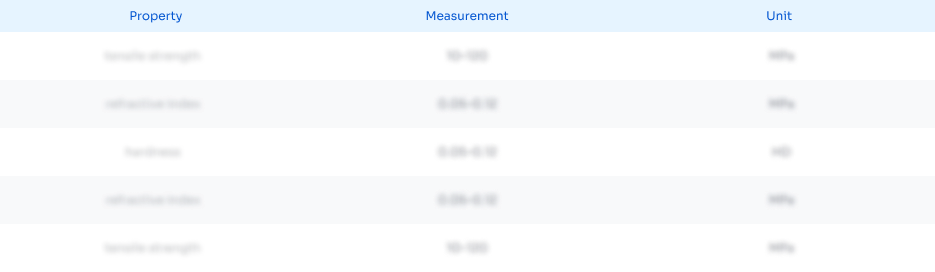
Abstract
Description
Claims
Application Information

- R&D
- Intellectual Property
- Life Sciences
- Materials
- Tech Scout
- Unparalleled Data Quality
- Higher Quality Content
- 60% Fewer Hallucinations
Browse by: Latest US Patents, China's latest patents, Technical Efficacy Thesaurus, Application Domain, Technology Topic, Popular Technical Reports.
© 2025 PatSnap. All rights reserved.Legal|Privacy policy|Modern Slavery Act Transparency Statement|Sitemap|About US| Contact US: help@patsnap.com