Special extruder for manufacturing rubber
An extruder and rubber technology, applied in the field of rubber manufacturing, can solve the problems of easy generation of bubbles, premature decomposition, waste of labor and other problems of rubber materials, and achieve the effect of improving heat exchange rate, avoiding premature melting, and improving product quality.
- Summary
- Abstract
- Description
- Claims
- Application Information
AI Technical Summary
Problems solved by technology
Method used
Image
Examples
Embodiment Construction
[0020] The present invention is described in further detail now in conjunction with accompanying drawing. These drawings are all simplified schematic diagrams, which only illustrate the basic structure of the present invention in a schematic manner, so they only show the configurations related to the present invention.
[0021] Such as figure 1 A special extruder for making rubber is shown, including a machine base 1, a controller part 6, a drive motor 4 and a reducer 5 are installed on the right side of the base 1, and a feed inlet and a temperature control part 2 are installed in the middle of the base 1 , the reducer 5 is connected with the driving motor 4 , the output shaft of the reducer 5 is connected with the screw device 3 and controlled by the controller part 6 .
[0022] Such as figure 2 and Figure 4 Shown is a special extruder for making rubber. The screw device 3 includes an outer cylinder 31 fixed on the machine base 1, an inner cylinder 32 arranged in the ou...
PUM
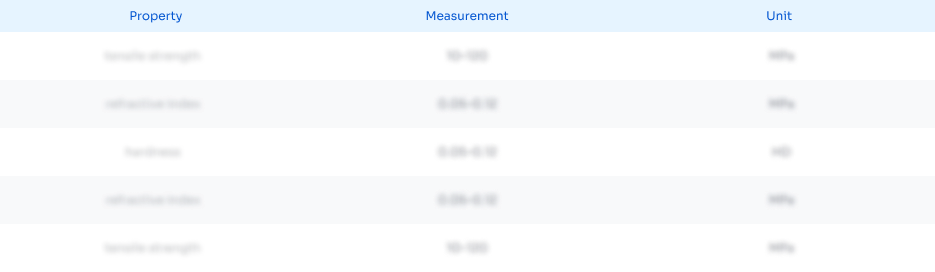
Abstract
Description
Claims
Application Information

- R&D
- Intellectual Property
- Life Sciences
- Materials
- Tech Scout
- Unparalleled Data Quality
- Higher Quality Content
- 60% Fewer Hallucinations
Browse by: Latest US Patents, China's latest patents, Technical Efficacy Thesaurus, Application Domain, Technology Topic, Popular Technical Reports.
© 2025 PatSnap. All rights reserved.Legal|Privacy policy|Modern Slavery Act Transparency Statement|Sitemap|About US| Contact US: help@patsnap.com