Preparation method of integral-type vacuum heat insulation and temperature preservation plate
A technology of vacuum insulation and thermal insulation board, which is applied in the directions of thermal insulation, insulation improvement, climate change adaptation, etc., can solve problems such as thermal insulation and energy saving effect affecting the progress and quality of construction projects, poor surface flatness, and easy generation of cold and hot bridges, etc. The effect of energy saving, heat preservation, size specification, and flatness improvement
- Summary
- Abstract
- Description
- Claims
- Application Information
AI Technical Summary
Problems solved by technology
Method used
Examples
Embodiment 1
[0024] A method for preparing an integral vacuum heat insulation board is carried out according to the following steps:
[0025] The first step, the production of the core board
[0026] a. Proportioning the raw materials of the core board according to the following parts by weight: 70 parts of microfiber, 15 parts of microporous material, 10 parts of semi-closed pore material and 5 parts of binder;
[0027] B, the raw material of described core material board and water are mixed and stirred into slurry by weight ratio of 2:1, then extruded to obtain molding core material board;
[0028] c. Dry the molded core board at a temperature of 400° C. for 5 minutes, then cut the dried molded core board and evenly punch a plurality of through holes with a diameter of 4 mm on the cut board surface to obtain Standard core board; the freeze-thaw resistance of the standard core board is greater than or equal to 0.1MPa, and the impact strength is not less than 2.0J;
[0029] The second st...
Embodiment 2
[0036] A method for preparing an integral vacuum heat insulation board is carried out according to the following steps:
[0037] The first step, the production of the core board
[0038] a. The raw materials of the core board are proportioned according to the following parts by weight: 55 parts of microfiber, 20 parts of microporous material, 15 parts of semi-closed pore material and 10 parts of binder;
[0039] B, the raw material of described core material board and water are mixed and stirred into slurry by weight ratio of 2:1, then extruded to obtain molding core material board;
[0040] c. Dry the molded core board at a temperature of 150° C. for 8 minutes, then cut the dried molded core board and evenly punch a plurality of through holes with a diameter of 3 mm on the cut board surface to obtain Standard core board; the freeze-thaw resistance of the standard core board is greater than or equal to 0.1MPa, and the impact strength is not less than 2.0J;
[0041] The secon...
Embodiment 3
[0048] A method for preparing an integral vacuum heat insulation board is carried out according to the following steps:
[0049] The first step, the production of the core board
[0050] a. The raw materials of the core board are proportioned according to the following parts by weight: 60 parts of superfine fibers, 15 parts of microporous materials, 18 parts of semi-closed-pore granular materials and 7 parts of binder;
[0051] B, the raw material of described core material board and water are mixed and stirred into slurry by weight ratio of 2:1, then extruded to obtain molding core material board;
[0052] c. Dry the molded core board at a temperature of 300° C. for 6 minutes, then cut the dried molded core board and evenly punch a plurality of through holes with a diameter of 4 mm on the cut board surface to obtain Standard core board; the freeze-thaw resistance of the standard core board is greater than or equal to 0.1MPa, and the impact strength is not less than 2.0J;
...
PUM
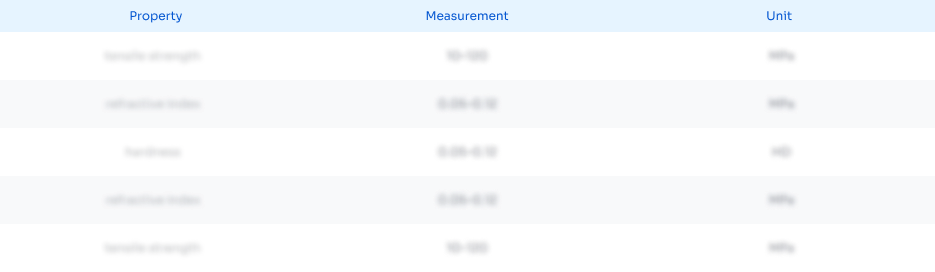
Abstract
Description
Claims
Application Information

- R&D
- Intellectual Property
- Life Sciences
- Materials
- Tech Scout
- Unparalleled Data Quality
- Higher Quality Content
- 60% Fewer Hallucinations
Browse by: Latest US Patents, China's latest patents, Technical Efficacy Thesaurus, Application Domain, Technology Topic, Popular Technical Reports.
© 2025 PatSnap. All rights reserved.Legal|Privacy policy|Modern Slavery Act Transparency Statement|Sitemap|About US| Contact US: help@patsnap.com