Hollow variable-diameter porous friction head and preparation method for surface composite material of metal material
A technology for surface composite materials and metal materials, which is applied in the field of preparing metal material surface composite materials by friction stir processing, can solve the problems of uneven distribution of reinforcement phases, particle splashing and moving, etc., to achieve increased processing range, uniform distribution and dispersion, The effect of broad application prospects
- Summary
- Abstract
- Description
- Claims
- Application Information
AI Technical Summary
Problems solved by technology
Method used
Image
Examples
specific Embodiment approach 1
[0014] Specific implementation mode one: combine figure 1 and figure 2 Describe this embodiment. The friction head of this embodiment includes a friction stirring body, a variable diameter plate 4 and eight sealing screws 5. The friction stirring body 1 is composed of an upper cylinder 1 and a lower cylinder 2. The upper cylinder 1 It is arranged up and down with the lower cylinder 2 and made into one body. The diameter of the upper cylinder 1 is smaller than the diameter of the lower cylinder 2. The outer surface of the upper cylinder 1 is provided with a clamping surface 1-1. The lower cylinder The lower end surface of 2 is a concave shoulder surface 2-1 whose outer edge is higher than the center, and the upper cylinder 1 and the lower cylinder 2 are provided with a channel 3 along the axis, and the channel 3 is divided into two sections from top to bottom, respectively It is the upper channel 3-1 and the middle channel 3-2. The channel 3 is used for the storage of the rei...
specific Embodiment approach 2
[0015] Specific implementation mode two: combination figure 1 To illustrate this embodiment, the inner diameter of each lower vertical channel 2-4 in this embodiment is smaller than the inner diameter of the middle channel 3-2. Other components and connections are the same as those in the first embodiment.
specific Embodiment approach 3
[0016] Specific implementation mode three: combination figure 1 Describe this implementation mode, this implementation mode is realized through the following steps:
[0017] Step 1. Determine the geometric size of the friction head: Determine the diameter D of the shoulder of the friction head according to the width of the primary surface composite materialization of the workpiece to be processed. The diameter D of the friction head shoulder is equal to the width of the primary surface composite materialization. The inner diameter of the channel 2-4 is 0.1D to 0.2D, and the outer edge of the concave shoulder surface 2-1 is 0.2mm to 1.5mm higher than the center of the concave shoulder surface 2-1; the width of the primary surface composite material is usually at 12mm~36mm, that is, the diameter D of the shoulder of the friction head is 12mm~36mm, when D=12mm, the inner diameter of the lower channel 3-3 is 0.17D (ie 2mm), when D=24mm, the inner diameter of the lower channel 3-3 ...
PUM
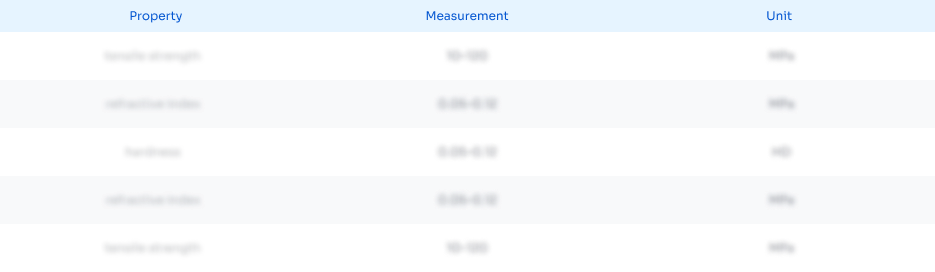
Abstract
Description
Claims
Application Information

- R&D Engineer
- R&D Manager
- IP Professional
- Industry Leading Data Capabilities
- Powerful AI technology
- Patent DNA Extraction
Browse by: Latest US Patents, China's latest patents, Technical Efficacy Thesaurus, Application Domain, Technology Topic, Popular Technical Reports.
© 2024 PatSnap. All rights reserved.Legal|Privacy policy|Modern Slavery Act Transparency Statement|Sitemap|About US| Contact US: help@patsnap.com