Horizontal oil-fired and gas-fired efficient energy-saving boiler
A high-efficiency, energy-saving and fuel-efficient technology, applied in the field of boilers, can solve the problems of increased manufacturing difficulty and production cost, increased boiler exterior design parameters, cracking of the front tube sheet of the re-combustion chamber, etc., and achieves good combustion conditions and saves equipment. Investment cost, effect of eliminating ventilation resistance
- Summary
- Abstract
- Description
- Claims
- Application Information
AI Technical Summary
Problems solved by technology
Method used
Image
Examples
Embodiment Construction
[0012] A horizontal oil-fired gas-fired high-efficiency energy-saving boiler, including a drum 14, the outer surface of the drum 14 is covered with an insulating layer 2, and the inside of the drum 14 is provided with a furnace 3 connected to the burner, and at the inner end of the furnace 3 A rear head 10 is provided, an explosion-proof device 9 is arranged at the rear head 10, a second return pipe 12 of an inner ring and a third return pipe 11 of an outer ring are arranged on the periphery of the furnace 3, and the front pipe of the drum 14 The front portion of the plate 15 is provided with a front smoke box 13, and the rear portion of the rear tube plate 16 of the drum 14 is provided with a rear smoke box 4, and the rear smoke box 4 is provided with a smoke outlet 5, and the front end of the second return pipe 12 is connected to the The front smoke box 13 is connected, and the rear end of the second return pipe 12 is arranged as an elbow, and the elbow at the rear end of the...
PUM
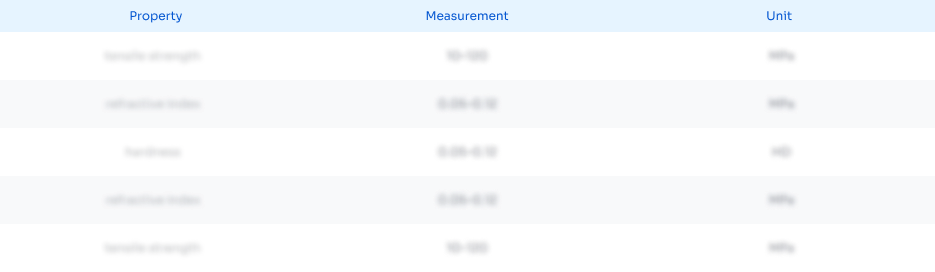
Abstract
Description
Claims
Application Information

- Generate Ideas
- Intellectual Property
- Life Sciences
- Materials
- Tech Scout
- Unparalleled Data Quality
- Higher Quality Content
- 60% Fewer Hallucinations
Browse by: Latest US Patents, China's latest patents, Technical Efficacy Thesaurus, Application Domain, Technology Topic, Popular Technical Reports.
© 2025 PatSnap. All rights reserved.Legal|Privacy policy|Modern Slavery Act Transparency Statement|Sitemap|About US| Contact US: help@patsnap.com