Rotating mechanism for excavator working device
A technology of working device and rotating mechanism, which is applied in the direction of mechanically driven excavators/dredgers, etc., can solve problems such as the inability of the body to rotate, and achieve the effects of simple structure, convenient operation and high excavation efficiency
- Summary
- Abstract
- Description
- Claims
- Application Information
AI Technical Summary
Problems solved by technology
Method used
Image
Examples
Embodiment 1
[0018] An excavator working device rotation mechanism in this embodiment includes a boom 1, a boom cylinder 2, a pinion shaft 3, a rack 4, a rotary cylinder 5, a rotary arm 6, a stick cylinder 7, a stick 8, a bucket Oil cylinder 9, rocker 10, connecting rod 11, bucket 12 and two guide sleeves 13; the boom 1 is hinged with the boom oil cylinder 2, the front part of the boom 1 is a cavity structure, and the front part of the boom 1 A pinion shaft 3, a rack 4 and two guide sleeves 13 are arranged in the inner cavity, and the pinion shaft 3 is placed on the front and rear two rolling bearings in the front cavity of the boom 1, and the front end of the gear shaft 3 is fixed to one end of the rotating arm 6. , the rack 4 meshes with the gear shaft 3, and the two sides of the rack 4 are covered by two guide sleeves 13 respectively, and can slide along the two guide sleeves 13, and the two guide sleeves are fixed on the bottom of the boom 1 by about 13 minutes. On the inner wall at bo...
PUM
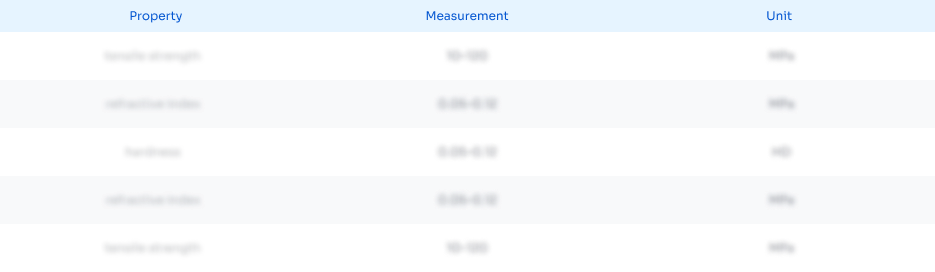
Abstract
Description
Claims
Application Information

- R&D Engineer
- R&D Manager
- IP Professional
- Industry Leading Data Capabilities
- Powerful AI technology
- Patent DNA Extraction
Browse by: Latest US Patents, China's latest patents, Technical Efficacy Thesaurus, Application Domain, Technology Topic, Popular Technical Reports.
© 2024 PatSnap. All rights reserved.Legal|Privacy policy|Modern Slavery Act Transparency Statement|Sitemap|About US| Contact US: help@patsnap.com