Multi-closed loop method introducing torque correction into high-precision tracking system
A tracking system and force introduction technology, applied in the field of tracking control, can solve the problems of speed fluctuation, torque fluctuation, low torque closed-loop bandwidth, etc., to achieve smooth motor speed, fast torque response, and meet the requirements of rapidity.
- Summary
- Abstract
- Description
- Claims
- Application Information
AI Technical Summary
Problems solved by technology
Method used
Image
Examples
Embodiment Construction
[0020] Firstly, some parameters of a high-precision tracking system are introduced as follows: This system uses a permanent magnet synchronous torque motor as an actuator. The parameters of the torque motor are as follows: stator resistance r = 2.125Ω; inductance L d = L q =11.6mH; number of poles p=12; moment coefficient K t =1.8Nm / A; the direct axis component of permanent magnet flux linkage is ψ dm = 0.1994Wb;
[0021] The transfer function of the mechanical part of the tracking system is:
[0022] G m ( s ) = 2.8 ( 4.788 e - 007 s 2 + 3.46 e - 005 s + ...
PUM
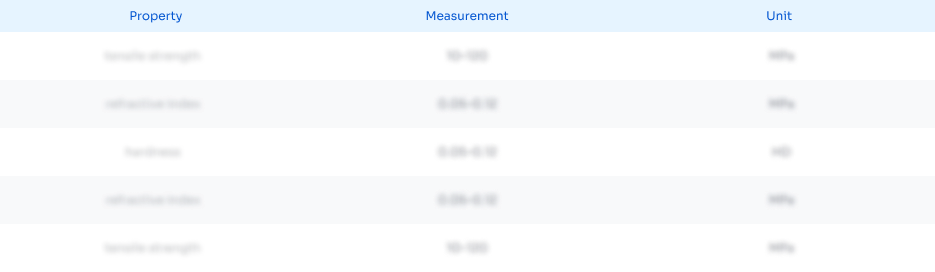
Abstract
Description
Claims
Application Information

- Generate Ideas
- Intellectual Property
- Life Sciences
- Materials
- Tech Scout
- Unparalleled Data Quality
- Higher Quality Content
- 60% Fewer Hallucinations
Browse by: Latest US Patents, China's latest patents, Technical Efficacy Thesaurus, Application Domain, Technology Topic, Popular Technical Reports.
© 2025 PatSnap. All rights reserved.Legal|Privacy policy|Modern Slavery Act Transparency Statement|Sitemap|About US| Contact US: help@patsnap.com