Chlorinated polyethylene rubber material
A technology of chlorinated polyethylene and rubber materials, applied in the field of rubber, can solve problems such as poor compression set performance, affecting product performance and appearance, and easy to produce orange peel phenomenon, so as to reduce compression set, good compression set, Good performance of rubber
- Summary
- Abstract
- Description
- Claims
- Application Information
AI Technical Summary
Problems solved by technology
Method used
Examples
Embodiment 1
[0015] The raw materials were weighed according to the following proportions: 37% chlorinated polyethylene, 31% carbon black, 13% trioctyl trimellitate, 8% vulcanizing agent (PDM), processing aids (internal release agent and microcrystalline wax mixture) 2%, magnesium oxide 7.2%, silicone active agent (octamethylcyclotetrasiloxane) 1.8%.
[0016] Adjust the temperature of the internal mixer to 60~70°C, add chlorinated polyethylene to the internal mixer—processing aid, magnesium oxide, silicon-oxygen active agent and mix for 1 minute—add carbon black and trioctyl trimellitate Ester—pressurize 12Mpa and knead—raise the top bolt when the temperature reaches 85°C, then pressurize 12Mpa to continue mixing, when the temperature reaches 100~110°C, remove glue—filter—add vulcanizing agent—inspect—— Stored in and parked for use, it is the chlorinated polyethylene rubber material sample prepared in the embodiment of the present invention.
[0017] The compression set performance test o...
Embodiment 2
[0019] The raw materials were weighed according to the following proportions: chlorinated polyethylene 36%; carbon black 30%; trioctyl trimellitate 12%; vulcanizing agent (PDM) 10%; processing aids (internal release agent and microcrystalline wax Arbitrary ratio mixture) 2.5%, magnesium oxide 8%; silicone active agent (octamethylcyclotetrasiloxane) 1.5%.
[0020] The preparation method is the same as in Example 1.
Embodiment 3
[0022] Weigh each raw material according to the following proportions: 37.5% chlorinated polyethylene, 31.5% carbon black, 13% trioctyl trimellitate, 7.5% vulcanizing agent (PDM), processing aids (internal release agent and microcrystalline wax Arbitrary ratio mixture) 2%, magnesium oxide 7%, silicone active agent (octamethylcyclotetrasiloxane,) 1.5%.
[0023] The preparation method is the same as in Example 1.
[0024] The following table compares the rubber material of the present invention (rear) with the existing rubber material of the same type (front) and various performance parameters required by the standards of this type of rubber material:
[0025] It can be seen from the above table that the rubber material of the present invention has excellent properties, especially the compression set is 68% (note: according to the PV3307 standard, the prior art is 87%), which greatly reduces the compression set, so that in the transport medium During the process, the perman...
PUM
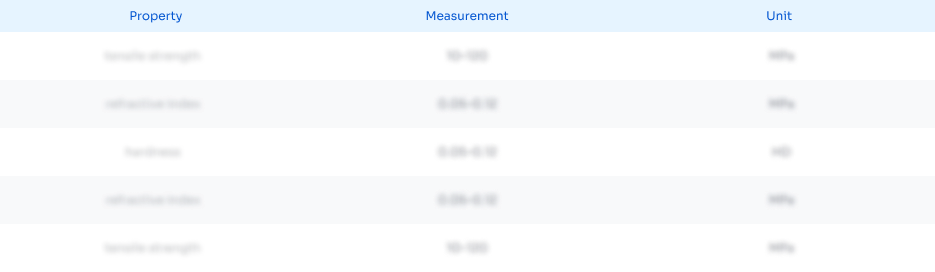
Abstract
Description
Claims
Application Information

- R&D
- Intellectual Property
- Life Sciences
- Materials
- Tech Scout
- Unparalleled Data Quality
- Higher Quality Content
- 60% Fewer Hallucinations
Browse by: Latest US Patents, China's latest patents, Technical Efficacy Thesaurus, Application Domain, Technology Topic, Popular Technical Reports.
© 2025 PatSnap. All rights reserved.Legal|Privacy policy|Modern Slavery Act Transparency Statement|Sitemap|About US| Contact US: help@patsnap.com