Sodium chromate alkali solution impurity removal method and preparation method of chromic oxide
An alkaline solution, sodium chromate technology, applied in the directions of chromium trioxide, chromium oxide/hydrate, chromate/dichromate, etc., can solve the problems of trivalent chromium loss, difficult to elute chromium, etc. The effect of high conversion rate, low cost and mild conditions
- Summary
- Abstract
- Description
- Claims
- Application Information
AI Technical Summary
Problems solved by technology
Method used
Image
Examples
Embodiment 1
[0039] Select sodium chromate alkaline solution from a chromium salt factory
[0040]
[0041] The alkaline solution obtained by calcium-free roasting is pumped into the first tank of the continuous carbon separation tank, and the temperature of the first tank is controlled to be 80°C. into CO 2 (high purity CO 2 Mix with air, volume fraction 55%), add aluminum hydroxide seed crystal, seed crystal coefficient is 0.3, carry out continuous carbonization, fully increase CO 2 utilization rate. The carbon final tank is separately fed into CO 2 , to fully precipitate the silicon in the solution. The cumulative decomposition time is 2h. The removal rate of carbon and aluminum is 99.9%, and the removal rate of silicon is 98.5%.
[0042] The aluminum slime obtained after carbon separation was countercurrently washed 4 times at a temperature of 80°C for 15 minutes. After carbon separation, the filtrate obtained by filtering is mixed with potato starch and pumped into continuou...
Embodiment 2
[0045] Select sodium chromate alkaline solution from a chromium salt factory
[0046]
[0047] The alkaline solution obtained by calcium-free roasting is pumped into the first tank of the continuous carbon separation tank, and the temperature of the first tank is controlled to be 90°C. into CO 2 (lime kiln gas, purification, compression, volume fraction 38%), add aluminum hydroxide seed crystals, the seed crystal coefficient is 0.2, carry out continuous carbonization, fully increase CO 2 utilization rate. The carbon final tank is separately fed into CO 2 , to fully precipitate the silicon in the solution. The cumulative decomposition time is 3h. The removal rate of carbon and aluminum is 99.9%, and the removal rate of silicon is 99.1%.
[0048] The aluminum slime obtained after carbon separation was countercurrently washed 4 times at a temperature of 80°C for 15 minutes. After carbon separation, the filtrate obtained by filtering is mixed with pregelatinized starch an...
Embodiment 3
[0051] Select sodium chromate alkaline solution from a chromium salt factory
[0052]
[0053] The alkaline solution obtained by calcium-free roasting is pumped into the first tank of the continuous carbon separation tank, and the temperature of the first tank is controlled to be 85°C. into CO 2 (calcination kiln gas, purification, compression, volume fraction 38%), adding aluminum hydroxide seed crystals, the seed crystal coefficient is 0.4, continuous carbon content, fully increase CO 2 utilization rate. The carbon final tank is separately fed into CO 2 , to fully precipitate the silicon in the solution. The cumulative decomposition time is 3.5h. The removal rate of carbon and aluminum is 99.9%, and the removal rate of silicon is 99.4%.
[0054] The aluminum slime obtained after carbon separation was countercurrently washed 4 times at a temperature of 80°C for 15 minutes. After carbon separation, the filtrate obtained by filtering is mixed with dextrin and pumped in...
PUM
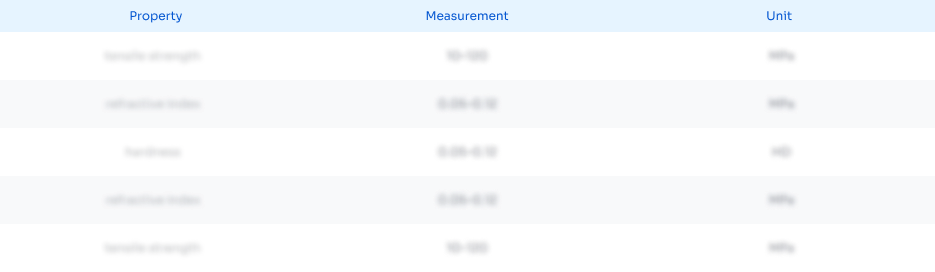
Abstract
Description
Claims
Application Information

- Generate Ideas
- Intellectual Property
- Life Sciences
- Materials
- Tech Scout
- Unparalleled Data Quality
- Higher Quality Content
- 60% Fewer Hallucinations
Browse by: Latest US Patents, China's latest patents, Technical Efficacy Thesaurus, Application Domain, Technology Topic, Popular Technical Reports.
© 2025 PatSnap. All rights reserved.Legal|Privacy policy|Modern Slavery Act Transparency Statement|Sitemap|About US| Contact US: help@patsnap.com