Circuit board forming method and circuit board
A molding method and circuit board technology, which is applied in the direction of printed circuit, printed circuit manufacturing, electrical components, etc., can solve the problems of circuit board large shape tolerance, circuit board scrapping, etc., and achieve the effect of reducing shape tolerance and precise control
- Summary
- Abstract
- Description
- Claims
- Application Information
AI Technical Summary
Problems solved by technology
Method used
Image
Examples
Embodiment Construction
[0021] The invention provides a method for forming a circuit board, which is characterized in that it comprises:
[0022] Step 11, determining the expansion and contraction coefficients of each cover plate located on a motherboard;
[0023] Step 12, according to the expansion and contraction coefficients, and using the designed and formed positioning holes or designed and formed positioning parts corresponding to each cover plate, the actual forming positioning hole or the actual forming positioning part is made in the non-functional area of each cover plate, the said The designed forming positioning hole or the designed forming positioning part is the corresponding forming positioning hole or forming positioning part of each cover board before expansion and contraction offset occurs, and the actual forming positioning hole or actual forming positioning part is the expansion and shrinkage of each cover plate. The corresponding forming positioning hole or forming positioning ...
PUM
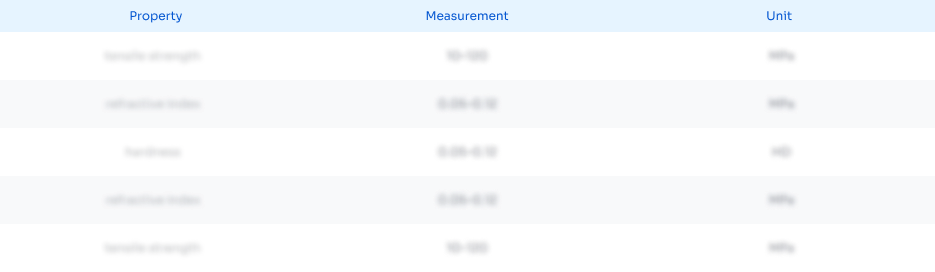
Abstract
Description
Claims
Application Information

- R&D
- Intellectual Property
- Life Sciences
- Materials
- Tech Scout
- Unparalleled Data Quality
- Higher Quality Content
- 60% Fewer Hallucinations
Browse by: Latest US Patents, China's latest patents, Technical Efficacy Thesaurus, Application Domain, Technology Topic, Popular Technical Reports.
© 2025 PatSnap. All rights reserved.Legal|Privacy policy|Modern Slavery Act Transparency Statement|Sitemap|About US| Contact US: help@patsnap.com