Five-axis numerical control interpolation method based on smooth compression of tool vectors
A vector compression and cutting tool technology, applied in the field of numerical control, can solve the problems of destroying the surface of the workpiece, increasing the transmission burden of the system, and large machining errors
- Summary
- Abstract
- Description
- Claims
- Application Information
AI Technical Summary
Problems solved by technology
Method used
Image
Examples
Embodiment Construction
[0043] The method of the present invention will be described in further detail below in conjunction with the accompanying drawings.
[0044] Such as figure 2 Shown, the inventive method comprises the following steps:
[0045] The five-axis numerical control interpolation method based on tool vector smooth compression of the present invention comprises the following steps:
[0046] According to the read-in NC machining program, judge whether any adjacent two tool vectors meet the conditions for continuous machining;
[0047] If the conditions for continuous processing are met, then perform tool vector compression interpolation and tool nose point position interpolation; (tool vector compression interpolation: for a continuous tool vector change area, use the Lagrange multiplier method to fit, in The interpolation between any two tool vectors can be realized on the fitted tool vector curve; the position interpolation of the tool tip point: the position interpolation of any two ...
PUM
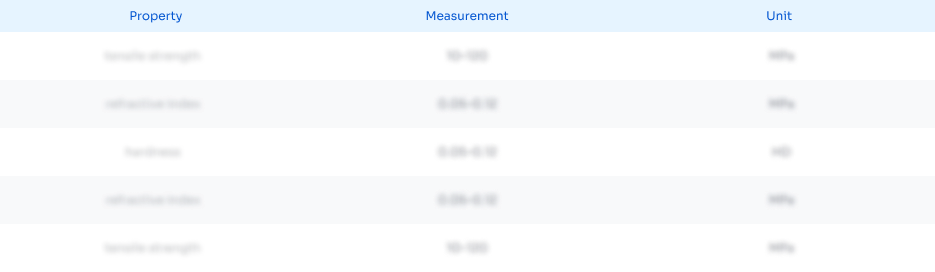
Abstract
Description
Claims
Application Information

- Generate Ideas
- Intellectual Property
- Life Sciences
- Materials
- Tech Scout
- Unparalleled Data Quality
- Higher Quality Content
- 60% Fewer Hallucinations
Browse by: Latest US Patents, China's latest patents, Technical Efficacy Thesaurus, Application Domain, Technology Topic, Popular Technical Reports.
© 2025 PatSnap. All rights reserved.Legal|Privacy policy|Modern Slavery Act Transparency Statement|Sitemap|About US| Contact US: help@patsnap.com