Undamped hydraulic yaw system based on pressure detection and control method of undamped hydraulic yaw system
A yaw system and non-damping technology, applied in the control of wind turbines, wind turbines, wind power generation, etc., can solve the problems of increased friction and wear at the brake caliper, high power waste, unit vibration and wind rotor blade fatigue, etc., to achieve Reduce friction and wear, avoid power waste, and improve damping effect
- Summary
- Abstract
- Description
- Claims
- Application Information
AI Technical Summary
Problems solved by technology
Method used
Image
Examples
Embodiment Construction
[0026] In order to facilitate the understanding of the specific principle and control method of the present invention, detailed embodiments of the system are described in detail through the accompanying drawings.
[0027] like figure 1 As shown, motor 1, oil pump 2, relief valve 3, oil tank 4, check valve 5, pressure relay 6, accumulator 7, accumulator safety valve group 8, proportional reversing valve 9, check valve 10, Relief valve 11, low-speed high-torque hydraulic motor 12, yaw gear 13, pressure sensor 14, yaw encoder 15, meshing ring gear 16 in the nacelle, yaw counter 17, wind speed and direction instrument 18 and connected to the oil pump and the Oil pipe L1 and oil pipe L2 between hydraulic motors.
[0028] The motor 1 drives the oil pump 2 to rotate to supply oil to the hydraulic yaw system; the outlet of the oil pump 2 is sequentially connected to one end of the overflow valve 3, the check valve 5, the accumulator 7, the pressure relay 6 and the proportional revers...
PUM
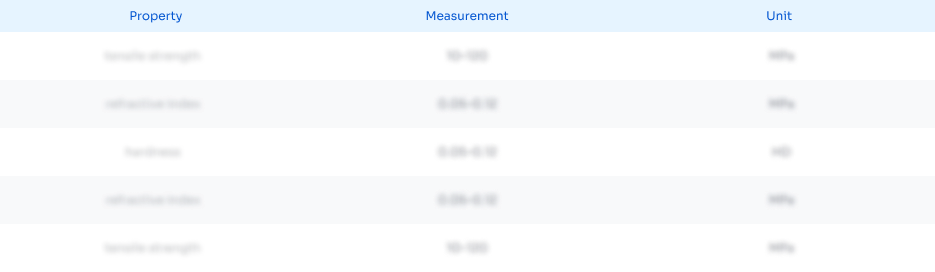
Abstract
Description
Claims
Application Information

- R&D
- Intellectual Property
- Life Sciences
- Materials
- Tech Scout
- Unparalleled Data Quality
- Higher Quality Content
- 60% Fewer Hallucinations
Browse by: Latest US Patents, China's latest patents, Technical Efficacy Thesaurus, Application Domain, Technology Topic, Popular Technical Reports.
© 2025 PatSnap. All rights reserved.Legal|Privacy policy|Modern Slavery Act Transparency Statement|Sitemap|About US| Contact US: help@patsnap.com