Novel three-degrees-of-freedom under-actuated mechanism
An underactuated, degree-of-freedom technology, applied in manipulators, program-controlled manipulators, manufacturing tools, etc., can solve the problems affecting the end effector's carrying capacity, large motion inertia, small carrying capacity, etc., and achieve compact structure, small size, and rigidity. Good results
- Summary
- Abstract
- Description
- Claims
- Application Information
AI Technical Summary
Problems solved by technology
Method used
Image
Examples
Embodiment 1
[0019] see figure 1 — image 3 , the new three-degree-of-freedom underactuated mechanism includes a base, a moving platform (11), three motion branch chains with the same structure symmetrically and uniformly arranged, two power sources and a position detection device, and is characterized in that: three motion branch chains The chains are respectively movably connected with the moving platform (11), which is not only convenient for processing and assembly but also flexible in movement; the moving platform (11) sinks toward the base and is concave in shape, which can make the structure more compact and enhance the rigidity of the mechanism; The two motors (3, 21) directly drive the two kinematic branch chains to form three kinematic branch chains for the under-actuated mechanism to make the moving platform (11) move in three degrees of freedom, reducing the cost and reducing the weight of the mechanism; The position detection device is connected with the under-actuated motion...
Embodiment 2
[0021] This embodiment is basically the same as Embodiment 1, and the special feature is that the structure of the base is: two motor support bases (2, 20) and a rotary encoder support base (12) are respectively fixed on a method by screws. On the upper surface of the blue plate (1), the two motor support seats (2, 20) and the rotary encoder support seat (12) are all spaced apart by 120°. The structure in which the moving platform (11) is movably connected with the three motion branch chains is: the first, second and third three moving platform connecting rods (10, 28, 19) are respectively fixed at the ends of the moving platform (11) by screws. On the lower surface, the three moving platform connecting rods (10, 28, 19) are evenly distributed in the circumferential direction of 120°, and the other ends of the three moving platform connecting rods (10, 28, 19) respectively pass through the first, second and third spherical pairs ( 9, 27, 18) are connected with the connecting r...
Embodiment 3
[0023] Such as figure 1As shown in -3, the new three-degree-of-freedom underactuated mechanism: the first motor (3) and the second motor (21) are respectively connected with the first reducer (4) and the second reducer (22) and pass through The bolt connection is fixed on the first motor support base (2) and the second motor support base (20), the rotary encoder (13) is fixed on the rotary encoder support base (12) through bolt connection, the first motor support base ( 2), the second motor support base (20) and the rotary encoder support base (12) are respectively fixed on the upper surface of the flange (1) by screws, the first motor support base (2), the second motor support base (20) ) and the rotary encoder support seat (12) are spaced 120° apart. One ends of the first, second and third moving platform connecting rods (10, 28, 19) are respectively fixed on the lower surface of the moving platform (11) by screws, and the three moving platform connecting rods (10, 28, ...
PUM
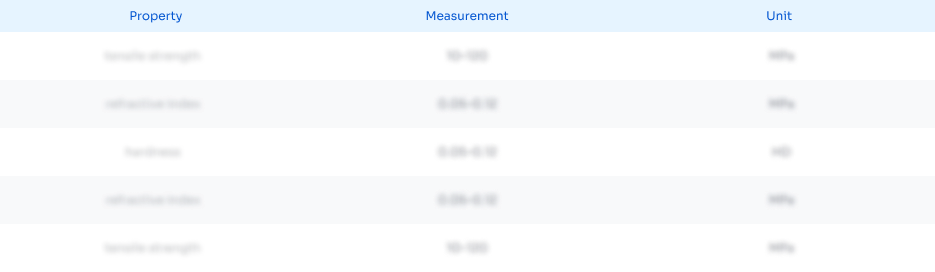
Abstract
Description
Claims
Application Information

- R&D
- Intellectual Property
- Life Sciences
- Materials
- Tech Scout
- Unparalleled Data Quality
- Higher Quality Content
- 60% Fewer Hallucinations
Browse by: Latest US Patents, China's latest patents, Technical Efficacy Thesaurus, Application Domain, Technology Topic, Popular Technical Reports.
© 2025 PatSnap. All rights reserved.Legal|Privacy policy|Modern Slavery Act Transparency Statement|Sitemap|About US| Contact US: help@patsnap.com