Manufacturing method of special-shaped hole at threads of thin wall part
A technology of thin-walled parts and special-shaped holes, which is applied in the field of thin-walled parts manufacturing, can solve the problems of complicated procedures, high cost, and the gas and liquid in the holes cannot be discharged smoothly, and achieves the effect of simple procedures and reduced processing costs.
- Summary
- Abstract
- Description
- Claims
- Application Information
AI Technical Summary
Problems solved by technology
Method used
Image
Examples
Embodiment Construction
[0018] Taking the processing of a countersunk screw as an example, the thread of the countersunk screw has a hexagonal hole, the width across the hexagon is 1.63mm, the depth of the hole is 3.00mm, the small thread diameter and the wall thickness of the hexagonal hole are only 0.53mm~0.58mm, see figure 2 and image 3 shown.
[0019] Adopt manufacturing method of the present invention to finish processing according to the following steps:
[0020] Step 1: Rolling thread, thread ring gauge, major diameter, minor diameter, middle diameter, root radius are all qualified.
[0021] Step 2: On an ordinary hexagonal lathe, use a Φ1.61mm drill bit to make a preparatory hole (cylindrical hole). The prepared preparatory hole has a diameter of Φ1.61mm~Φ1.62mm and a depth of 4.3mm~4.5mm.
[0022] Step 3: After making the preparatory hole, directly make the hexagonal hole, choose a special hexagonal punch with a width across the side of 1.64mm for processing special-shaped holes in the th...
PUM
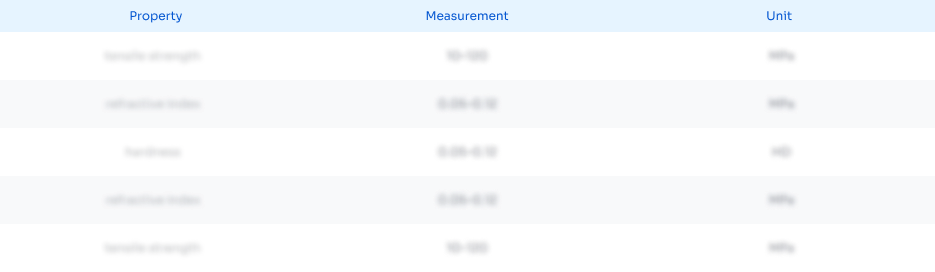
Abstract
Description
Claims
Application Information

- R&D
- Intellectual Property
- Life Sciences
- Materials
- Tech Scout
- Unparalleled Data Quality
- Higher Quality Content
- 60% Fewer Hallucinations
Browse by: Latest US Patents, China's latest patents, Technical Efficacy Thesaurus, Application Domain, Technology Topic, Popular Technical Reports.
© 2025 PatSnap. All rights reserved.Legal|Privacy policy|Modern Slavery Act Transparency Statement|Sitemap|About US| Contact US: help@patsnap.com