Making method of moving sliding plate
A production method and skateboard technology, which is applied in the field of plastic processing, can solve problems such as high equipment requirements and complex manufacturing process of sports skateboards, and achieve the effects of firm structure, easy manipulation, and reduced resistance
- Summary
- Abstract
- Description
- Claims
- Application Information
AI Technical Summary
Problems solved by technology
Method used
Image
Examples
Embodiment 1
[0040] Embodiment one: if Figure 1 to Figure 8 As shown, the manufacturing method of the sports skateboard of the present embodiment includes the following steps:
[0041] 1. Foam the EPS material in a foaming mold at a temperature of 100°C for 5 minutes to form a foam board;
[0042] 2. Cool the foaming mold with the foamed board with water, then take out the foamed board, then cool the foamed board to normal temperature naturally, and then dry the foamed board cooled to normal temperature at a temperature of 45°C;
[0043] 3. Wrap the outer surface of the dried foam board with glass fiber cloth, and then spray or coat the outer surface of the foam board wrapped with cloth with epoxy resin;
[0044] 4. Put the foamed board sprayed or coated with epoxy resin at room temperature to solidify to form a core board, and then polish the core board 1 smoothly to form a rough embryo of a sports skateboard;
[0045] 5. Wrap the outer surface of the polished rough skateboard with gla...
Embodiment 2
[0050] Embodiment two: if Figure 1 to Figure 8 As shown, the manufacturing method of the sports skateboard of the present embodiment includes the following steps:
[0051] 1. Foam the EPS material in a foaming mold at a temperature of 140°C for 3 minutes to form a foam board;
[0052] 2. Cool the foaming mold with the foamed board with water, then take out the foamed board, then cool the foamed board to normal temperature naturally, and then dry the foamed board cooled to normal temperature at a temperature of 55°C;
[0053] 3. Wrap the outer surface of the dried foam board with glass fiber cloth, and then spray or coat the outer surface of the foam board wrapped with cloth with epoxy resin;
[0054] 4. Put the foamed board sprayed or coated with epoxy resin at room temperature to solidify to form a core board, and then polish the core board 1 smoothly to form a rough embryo of a sports skateboard;
[0055] 5. Wrap the outer surface of the polished rough skateboard with gla...
Embodiment 3
[0060] Embodiment three: as Figure 1 to Figure 8 As shown, the manufacturing method of the sports skateboard of the present embodiment includes the following steps:
[0061] 1. Foam the EPS material in a foaming mold at a temperature of 180°C for 2 minutes to form a foam board;
[0062] 2. Cool the foaming mold with the foamed board with water, then take out the foamed board, then cool the foamed board to normal temperature naturally, and then dry the foamed board cooled to normal temperature at a temperature of 65°C;
[0063] 3. Wrap the outer surface of the dried foam board with glass fiber cloth, and then spray or coat the outer surface of the foam board wrapped with cloth with epoxy resin;
[0064] 4. Put the foamed board sprayed or coated with epoxy resin at room temperature to solidify to form a core board, and then polish the core board 1 smoothly to form a rough embryo of a sports skateboard;
[0065] 5. Wrap the outer surface of the polished rough skateboard with g...
PUM
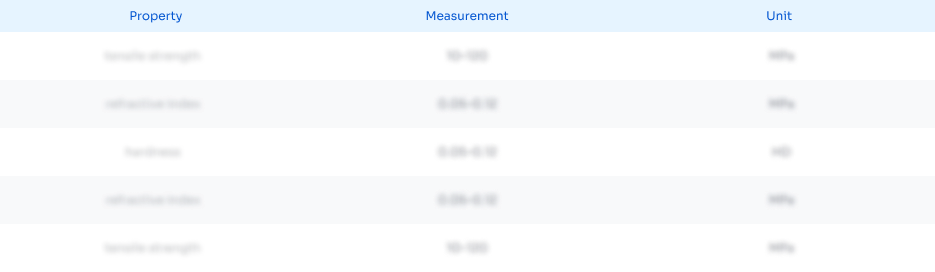
Abstract
Description
Claims
Application Information

- R&D
- Intellectual Property
- Life Sciences
- Materials
- Tech Scout
- Unparalleled Data Quality
- Higher Quality Content
- 60% Fewer Hallucinations
Browse by: Latest US Patents, China's latest patents, Technical Efficacy Thesaurus, Application Domain, Technology Topic, Popular Technical Reports.
© 2025 PatSnap. All rights reserved.Legal|Privacy policy|Modern Slavery Act Transparency Statement|Sitemap|About US| Contact US: help@patsnap.com