Manufacture method of super capacitor
A technology for supercapacitors and manufacturing methods, which is applied in the manufacture of hybrid/electric double layer capacitors, etc., which can solve the problems of low bond strength between collectors and pole pieces, and low bond strength of pole pieces, so as to achieve easy continuous production and mechanical The effect of high strength and soft electrode
- Summary
- Abstract
- Description
- Claims
- Application Information
AI Technical Summary
Problems solved by technology
Method used
Examples
Embodiment 1
[0023] The composite binder used in this embodiment is formed by mixing substances with the following general formula (1) and polytetrafluoroethylene:
[0024] [NH-R-CO-R-CO] x (1)
[0025] where x=100, R:C 2 h 4 , n=2
[0026] The content of each component in the composite binder is based on the mass ratio, the substance of the general formula (1) is 30%, and the polytetrafluoroethylene is 70%.
[0027] (1) Prepare the collector: roughen the metal aluminum surface by AC corrosion to obtain a collector with a thickness of 30 μm and a roughness of 3 μm on one side;
[0028] (2) Preparation of pole piece: mix the active material and conductive material evenly, dissolve the composite binder in isopropanol and disperse evenly to form a composite binder solution, add it to the above mixed materials and disperse evenly to form a mixture , wherein by mass percentage, the composite binder content is 2%, the active material is 92%, and the conductive material is 6%, and t...
Embodiment 2
[0038] The composite binder used in this embodiment is formed by mixing substances with the following general formula (1) and polytetrafluoroethylene:
[0039] [NH-R-CO-R-CO] x (1)
[0040] where x=200, R:C 3 h 6 , n=3
[0041] The mass ratio of each component in the composite binder is: 35% of the substance of the general formula (1), and 65% of polytetrafluoroethylene.
[0042] (1) Prepare the collector: roughen the surface of the aluminum alloy by AC corrosion to obtain a collector with a thickness of 30 μm and a roughness of 3 μm on one side;
[0043] (2) Preparation of pole piece: mix the active material and conductive material evenly, dissolve the composite binder in isopropanol and disperse evenly to form a composite binder solution, add it to the above mixed materials and disperse evenly to form a mixture , wherein by mass percentage, the composite binder content is 2%, the active material is 91%, and the conductive material is 7%, and then the above mixt...
Embodiment 3
[0053] The composite binder used in this embodiment is formed by mixing substances with the following general formula (1) structure and polytetrafluoroethylene:
[0054] [NH-R-CO-R-CO] x (1)
[0055] where x=300, R:C 4 h 8 , n=4
[0056] The mass ratio of each component in the composite binder is: 40% of the substance of the general formula (1), 60% of polytetrafluoroethylene.
[0057] (1) Prepare the collector: conduct AC corrosion roughening on the surface of the metal aluminum to obtain a collector with a thickness of 20 μm and a roughness of 2 μm on one side;
[0058] (2) Preparation of pole piece: mix the active material and the conductive material evenly, dissolve the composite binder in ethanol and disperse evenly to form a composite binder solution, add it to the above-mentioned mixed materials and disperse evenly to form a mixture, wherein By mass percentage, the composite binder content is 1.5%, the active material is 92.5%, and the conductive material...
PUM
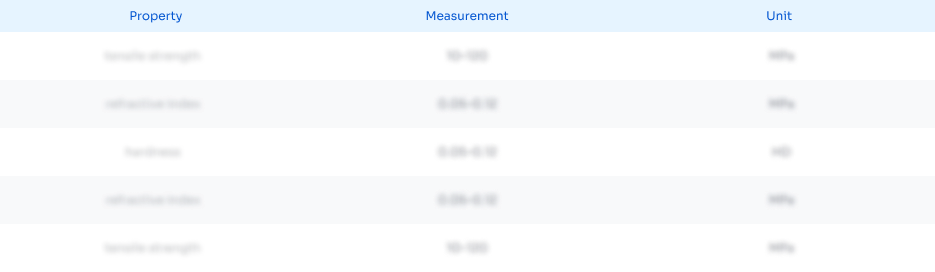
Abstract
Description
Claims
Application Information

- Generate Ideas
- Intellectual Property
- Life Sciences
- Materials
- Tech Scout
- Unparalleled Data Quality
- Higher Quality Content
- 60% Fewer Hallucinations
Browse by: Latest US Patents, China's latest patents, Technical Efficacy Thesaurus, Application Domain, Technology Topic, Popular Technical Reports.
© 2025 PatSnap. All rights reserved.Legal|Privacy policy|Modern Slavery Act Transparency Statement|Sitemap|About US| Contact US: help@patsnap.com