Three-section type heating and roasting method for refining vanadium pentoxide
A vanadium pentoxide, three-stage technology, which is applied in the field of three-stage heating and roasting, can solve the problems that the roasting temperature is difficult to control, affects production efficiency, and the conversion rate of vanadium is low, so that the roasting temperature is easy to control, the pollution is small, The effect of high conversion rate of vanadium
- Summary
- Abstract
- Description
- Claims
- Application Information
AI Technical Summary
Problems solved by technology
Method used
Examples
Embodiment 1
[0045] The calorific value of the raw ore is 850 kcal per kilogram, and the raw material with a particle size of less than 10 mm is prepared after crushing. The raw materials first enter the circulating fluidized bed boiler for heating and preliminary decarburization, and the high-temperature decarburized slag enters the first-stage roasting chamber at a temperature higher than 740 degrees Celsius. The first-stage roasting chamber can be filled to 90% of the volume, and the first The pressure air is injected into the raw materials in the first-stage roasting chamber to continue to fully burn the residual carbon in the materials. By controlling the amount of air injected into different parts of the materials, the discharge temperature is controlled at 800-950 degrees Celsius; the materials in the first-stage roasting chamber pass through about 2 After about an hour of deep decarburization and preliminary roasting, the material enters the second-stage roasting chamber at a temper...
Embodiment 2
[0047] On the basis of Example 1, a heat dissipation device and a stirring device are arranged in the first-stage roasting chamber, and the heat dissipation device and the stirring device in the first-stage roasting chamber are controlled to control the roasting temperature and prevent the material from coking.
Embodiment 3
[0049] On the basis of Example 1, a stirring device is set in the second-stage roasting chamber, and the stirring device in the second-stage roasting chamber is controlled to control the temperature of the oxygen-enriched pressure roasting and prevent the material from coking.
PUM
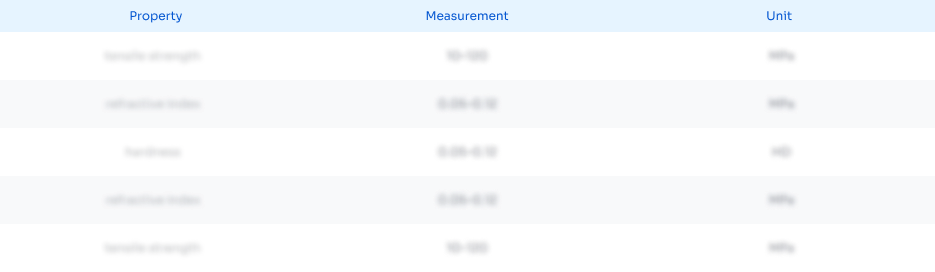
Abstract
Description
Claims
Application Information

- R&D
- Intellectual Property
- Life Sciences
- Materials
- Tech Scout
- Unparalleled Data Quality
- Higher Quality Content
- 60% Fewer Hallucinations
Browse by: Latest US Patents, China's latest patents, Technical Efficacy Thesaurus, Application Domain, Technology Topic, Popular Technical Reports.
© 2025 PatSnap. All rights reserved.Legal|Privacy policy|Modern Slavery Act Transparency Statement|Sitemap|About US| Contact US: help@patsnap.com