Smelting process for production of super-low sulphur steel
A technology of ultra-low sulfur and process route, which is applied to realize the stable control of sulfur content in steel when smelting ultra-low-sulfur steel. In the field of ultra-low-sulfur steel production, it can solve problems such as difficulty in meeting mass production, unstable control, and failure to find , to achieve the effect of stable control
- Summary
- Abstract
- Description
- Claims
- Application Information
AI Technical Summary
Problems solved by technology
Method used
Examples
Embodiment 1
[0018] Steel type X52MS, the target sulfur content of the finished product is less than 0.0012%. The adopted process route is: hot metal spraying magnesium desulfurization pretreatment-converter-ladle powder spraying-LF furnace refining-RH refining-continuous casting.
[0019] Desulfurization pretreatment of molten iron spraying magnesium: Desulfurization by spraying granular magnesium, removing desulfurization slag after desulfurization, [S] in molten iron after desulfurization = 0.005%.
[0020] Converter smelting: Converter smelting controls the sulfur content of steel scrap to 0.008%; the sulfur content in the lime ash of converter slagging material is 0.040% (weight percentage); the end temperature of converter is T=1680℃, [S]=0.0090%; , the addition amount is 4.5kg / t steel; after tapping, aluminum grains are added to the slag surface of the ladle to deoxidize the slag surface, and the addition amount is 0.5kg / t steel.
Embodiment 2
[0027] The steel type is X65MS, and the target sulfur content of the finished product is less than 0.0010%. The process route adopted is: molten iron magnesium spraying desulfurization pretreatment-converter-ladle powder spraying-LF furnace refining-RH refining-continuous casting.
[0028] Desulfurization pretreatment of hot metal spraying with magnesium: spraying granular magnesium for desulfurization, removing desulfurization slag after desulfurization, [S] in molten iron after desulfurization = 0.004%.
[0029] Converter smelting: Converter smelting controls the sulfur content of steel scrap to ≤0.006%; the sulfur content in the lime ash of converter slagging material is 0.035% (percentage by weight); the end point temperature of converter is T=1690℃, [S]=0.0070%; For deoxidation, the addition amount is 6.0kg / t steel; after tapping, aluminum particles are added to the slag surface of the ladle for deoxidation on the slag surface, and the addition amount is 0.6kg / t steel.
...
PUM
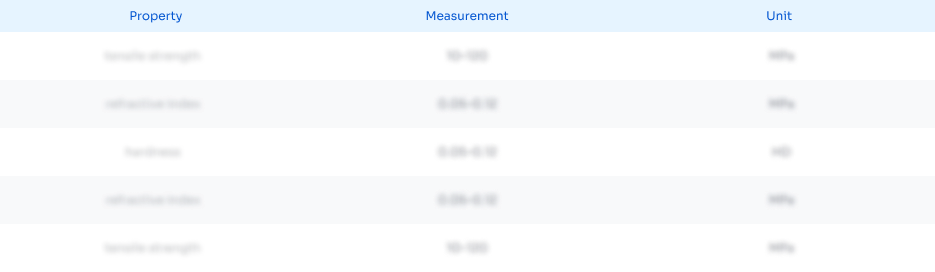
Abstract
Description
Claims
Application Information

- R&D
- Intellectual Property
- Life Sciences
- Materials
- Tech Scout
- Unparalleled Data Quality
- Higher Quality Content
- 60% Fewer Hallucinations
Browse by: Latest US Patents, China's latest patents, Technical Efficacy Thesaurus, Application Domain, Technology Topic, Popular Technical Reports.
© 2025 PatSnap. All rights reserved.Legal|Privacy policy|Modern Slavery Act Transparency Statement|Sitemap|About US| Contact US: help@patsnap.com