High-temperature molten steel slag treating method
A technology of liquid steel slag and a treatment method, which is applied in the field of waste steel slag recycling, can solve the problems of inability to use liquid steel slag for atomization treatment, unable to adjust the fluidity of steel slag, etc., and achieves wide source of raw materials, good steel slag stability, and improved application range. Effect
- Summary
- Abstract
- Description
- Claims
- Application Information
AI Technical Summary
Problems solved by technology
Method used
Examples
Embodiment 1
[0021] The original steel slag is selected from the steel slag of Jinan Iron and Steel Group, and its chemical composition is CaO 38.96%, SiO 2 13.27%, Fe 2 o 3 22.62%, FeO 9.17%, Al 2 o 3 1.59%, MgO 6.68%, free calcium oxide 2.6%, free magnesium oxide 6.68%, other 6.52%.
[0022] According to the composition of steel slag: CaO: SiO 2 = =3.15:1;
[0023] CaO: SiO 2 :Al 2 o 3 = ;
[0024] In 1000kg steel slag, CaO: 1000000×0.3896 / 56=6957 (mol);
[0025] SiO 2 :1000000×0.1327 / 60=2211.7 (mol);
[0026] Given the slag content and CaO:SiO 2 =2.5-3:1 is the closest, so the configuration of improver should be based on this. The target ratio is 3:1, and the amount of improver added is 1% of the mass of steel slag, which is 10kg.
[0027] Calculate the CaO and SiO that need to be added in 1000kg steel slag 2 The masses are 2624g and 7376g respectively.
[0028] Weigh 2624g CaO and 7376g SiO 2 , were crushed to below 5 mesh, and then mixed evenly and ...
Embodiment 2
[0031] The chemical composition of the original steel slag is CaO 40.32%, SiO 2 28.32%, FeO8.2%, Al 2 o 3 2.21%, MgO 5.0%, free calcium oxide 12.3%, free magnesium oxide 3.5%, other 1.5%.
[0032] According to the composition of steel slag: CaO: SiO 2 = =1.53:1;
[0033] CaO: SiO 2 :Al 2 o 3 = ;
[0034] In 1000kg steel slag, CaO: 1000000×0.4032 / 56=7200 (mol);
[0035] SiO 2 :1000000×0.2832 / 60=4720 (mol);
[0036] Al 2 o 3 : 1000000×0.024 / 102=235.3 (mol);
[0037] Given the slag content and CaO:SiO 2 :Al 2 o 3 =25-30: 15-25:1 is the closest, so the target ratio is set to CaO:SiO 2 :Al 2 o 3 =30:21:1, the amount of modifier added is 5% of the steel slag mass, which is 50kg;
[0038] Calculate the CaO and SiO that need to be added in 1000kg steel slag 2 and Al 2 o 3 The masses are 16750g, 31762g and 1488g respectively;
[0039] Weigh 16750g CaO, 31762g SiO 2 and 1488g Al 2 o 3 , were crushed to less than 5 mesh, and then ...
Embodiment 3
[0042] The chemical composition of the original steel slag is CaO 39.5%, SiO 2 16.8%, FeO17.2%, Al 2 o 3 2.4%, MgO 6.8%, free calcium oxide 10.3%, free magnesium oxide 6.5%, others, 0.5%.
[0043] According to the composition of steel slag: CaO: SiO 2 = =2.52:1;
[0044] CaO: SiO 2 :Al 2 o 3 = ;
[0045] In 1000kg steel slag, CaO: 1000000*0.395 / 56=7053.6 (mol);
[0046] SiO 2 :1000000×0.168 / 60=2800 (mol);
[0047] Al 2 o 3 : 1000000×0.024 / 102=235.3 (mol);
[0048] For raw steel slag CaO: SiO 2 :Al 2 o 3 =30: 11.9:1 and CaO: SiO 2 =2.52:1, so the selected target ratio is CaO:SiO 2 =2.4:1, the amount of modifier added is 2.5% of the steel slag mass, which is 25kg.
[0049] Calculate the CaO and SiO that need to be added in 1000kg steel slag 2 and Al 2 o 3 The masses of are 11518g and 13482g respectively;
[0050] Weigh 11518g CaO and 13482g SiO 2 , crushed to less than 5 meshes, and then mixed uniformly to make a modifier for use; take 1000kg of liq...
PUM
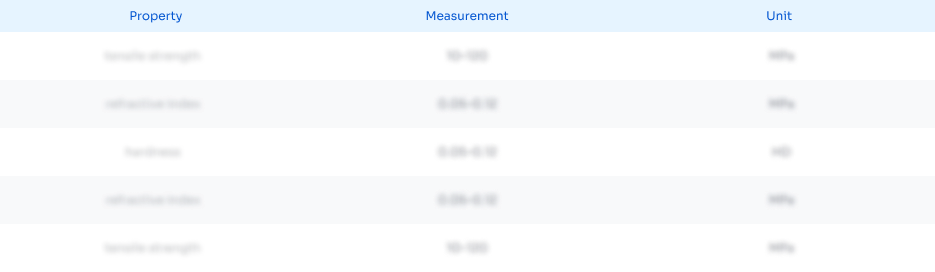
Abstract
Description
Claims
Application Information

- Generate Ideas
- Intellectual Property
- Life Sciences
- Materials
- Tech Scout
- Unparalleled Data Quality
- Higher Quality Content
- 60% Fewer Hallucinations
Browse by: Latest US Patents, China's latest patents, Technical Efficacy Thesaurus, Application Domain, Technology Topic, Popular Technical Reports.
© 2025 PatSnap. All rights reserved.Legal|Privacy policy|Modern Slavery Act Transparency Statement|Sitemap|About US| Contact US: help@patsnap.com