Pultrusion production process for nylon-based fiber reinforced thermo plastics
A production process and thermoplastic technology, applied in the pultrusion production process of nylon-based thermoplastic FRP, can solve the problems of fast polymerization rate, difficulty in pultrusion process, poor storage stability of impregnation solution, etc., and achieve good product performance, good impregnation effect, The effect of saving production cost
- Summary
- Abstract
- Description
- Claims
- Application Information
AI Technical Summary
Problems solved by technology
Method used
Image
Examples
Embodiment 1
[0051] 100 parts by weight of caprolactam and 15 parts by weight of nylon 6 with a number average molecular weight of 18,000 are added to the dehydration kettle (shown in 1) through the hopper (shown in 3), and the nitrogen valve (shown in 2) is opened, and the nitrogen bottle (shown in 14 (shown) to empty the air in the dehydration kettle, start the agitator (shown in 4), heat to 190°C, and after nylon 6 dissolves, cool down to 140°C to form a thickening slurry.
[0052] Add 1 part by weight of sodium hydroxide, 0.5 parts by weight of simethicone oil, and 1 part by weight of 500-mesh graphite powder into the above-mentioned thickening solution, start the vacuum pump (shown in 5), and vacuumize to keep the slurry in a boiling state. Dehydration, the temperature is controlled at 140°C, the extracted moisture and a small amount of caprolactam are stored in the reflux buffer tank (shown in 6), after dehydration for 15 minutes, the temperature of the material is lowered to 75°C, an...
Embodiment 2
[0060] Add 100 parts by weight of caprolactam and 10 parts by weight of nylon 66 with a number-average molecular weight of 23,000 to the dehydration kettle through a hopper. After the air in the dehydration kettle is evacuated with nitrogen, start the agitator and heat to 210°C until the nylon 66 is dissolved. Afterwards, the temperature was lowered to 135°C to form a viscosified slurry.
[0061] Add 1 part by weight of sodium hydroxide, 0.5 parts by weight of simethicone, and 1 part by weight of zinc stearate to the above-mentioned thickening solution, start the vacuum pump, keep the slurry in a boiling state for dehydration, and control the temperature at 135°C, after dehydration for 20 minutes, cool the material to 80°C, then discharge the material into the activation tank, the temperature of the activation tank is maintained at 75°C, and keep stirring continuously.
[0062] Toluene diisocyanate is used as the activator, and 0.3 parts by weight of toluene diisocyanate is in...
Embodiment 3
[0069] Add 100 parts by weight of caprolactam and 12 parts by weight of nylon 46 with a number average molecular weight of 23,000 to the dehydration kettle, vent the air in the kettle with nitrogen, start the stirrer, heat to 200°C, and cool down to 200°C after the nylon 46 is completely dissolved. At 130°C, a thickened slurry was formed.
[0070] Add 1 part by weight of potassium hydroxide, 0.5 parts by weight of magnesium stearate, and 0.5 parts by weight of simethicone to the thickening solution, start the vacuum pump, and vacuumize to keep the slurry in a boiling state for dehydration. The temperature is controlled at 130 ° C, dehydration 25 After a few minutes, the temperature of the material was lowered to 80° C., and then the material was discharged into the activation tank through a metering pump. The temperature of the activation tank was maintained at 80° C. and kept stirring.
[0071] Dicyclohexylmethane diisocyanate is used as the activator, and 0.2 parts by weight...
PUM
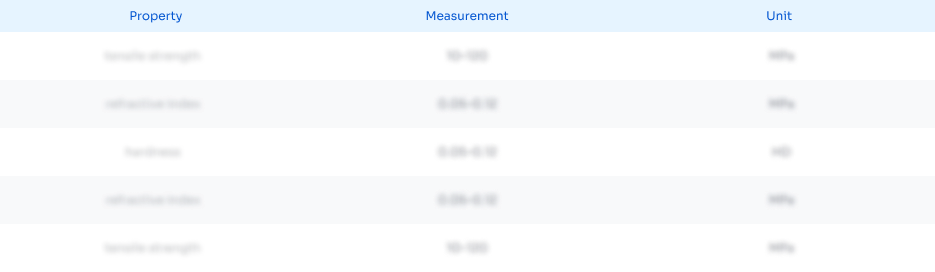
Abstract
Description
Claims
Application Information

- R&D
- Intellectual Property
- Life Sciences
- Materials
- Tech Scout
- Unparalleled Data Quality
- Higher Quality Content
- 60% Fewer Hallucinations
Browse by: Latest US Patents, China's latest patents, Technical Efficacy Thesaurus, Application Domain, Technology Topic, Popular Technical Reports.
© 2025 PatSnap. All rights reserved.Legal|Privacy policy|Modern Slavery Act Transparency Statement|Sitemap|About US| Contact US: help@patsnap.com