Method for preparing large-grain spherical praseodymium neodymium oxide
A praseodymium neodymium oxide, large particle technology, applied in chemical instruments and methods, inorganic chemistry, rare earth metal compounds, etc., can solve the problem of high production cost, achieve uniform particle distribution, good dispersibility, and easy control of the preparation process.
- Summary
- Abstract
- Description
- Claims
- Application Information
AI Technical Summary
Problems solved by technology
Method used
Image
Examples
Embodiment 1
[0011] Add 1000L praseodymium neodymium chloride solution with a concentration of 0.23mol / L into the FK3000 enamel reaction tank, heat the praseodymium neodymium chloride solution to 93°C, add 300L ammonium bicarbonate solution with a concentration of 2.5mol / L, and the precipitation reaction is completed in 3 hours. Insulated and aged for 1 hour, washed and filtered to obtain a precipitate of NdPr basic carbonate, which was kept at 1000°C for 4 hours in a firing kiln to obtain a NdPr oxide product with a central particle size of 28.11 μm.
Embodiment 2
[0013] Add 1000L praseodymium neodymium chloride solution with a concentration of 0.35mol / L into the FK3000 enamel reaction tank, heat the praseodymium neodymium chloride solution to 93°C, add 450L ammonium bicarbonate solution with a concentration of 2.5mol / L, and the precipitation reaction is completed in 3 hours. Insulated and aged for 1 hour, washed and filtered to obtain a precipitate of NdPr basic carbonate, which was kept at 1000° C. for 4 hours in a firing kiln to obtain a NdPr oxide product with a central particle size of 25.53 μm.
Embodiment 3
[0015] Add 1000L praseodymium neodymium chloride solution with a concentration of 0.18mol / L into the FK3000 enamel reaction tank, heat the praseodymium neodymium chloride solution to 93°C, add 240L ammonium bicarbonate solution with a concentration of 2.5mol / L, and the precipitation reaction is completed in 3 hours. Insulated and aged for 1 hour, washed and filtered to obtain a precipitate of NdPr basic carbonate. The NdPr basic carbonate was kept at 1000°C for 4 hours in a firing kiln to obtain a NdPr oxide product with a central particle size of 28.064 μm.
PUM
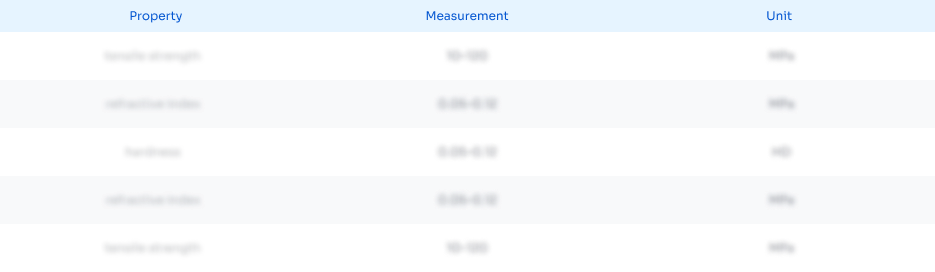
Abstract
Description
Claims
Application Information

- R&D
- Intellectual Property
- Life Sciences
- Materials
- Tech Scout
- Unparalleled Data Quality
- Higher Quality Content
- 60% Fewer Hallucinations
Browse by: Latest US Patents, China's latest patents, Technical Efficacy Thesaurus, Application Domain, Technology Topic, Popular Technical Reports.
© 2025 PatSnap. All rights reserved.Legal|Privacy policy|Modern Slavery Act Transparency Statement|Sitemap|About US| Contact US: help@patsnap.com