Film winding device and method for making optical film employing the same
A manufacturing method and technology of optical film, which are applied in the direction of winding strip, transportation and packaging, thin material processing, etc., can solve the problems of insufficient winding device, increased jitter, unable to prevent scratches, etc. The effect of attracting pressure and preventing winding misalignment
- Summary
- Abstract
- Description
- Claims
- Application Information
AI Technical Summary
Problems solved by technology
Method used
Image
Examples
Embodiment 1
[0133] For the winding device that passed the conditions of the following experiments 1 to 3, the figure 1 A cellulose triacetate film with a width of 2000 mm and a thickness of 80 μm produced in the film production line of the company was wound up.
[0134] (winding condition)
[0135] Experiment 1... is the case of winding without using the backup roll 30 and the suction nozzle 32.
[0136] Experiment 2... is the case where the winding device 10 of this embodiment demonstrated above was used. The gap L1 between the support roll 30 surface and the surrounding roll object 28 is 3 mm, the gap L2 between the support roll 30 surface and the side surface 32B of the support roll side of the suction nozzle 32 is 5 mm, and the side surface of the suction nozzle 32 surrounding the roll object 28 side The gap L3 between 32C and the surface of the surrounding roll 28 is 5mm. Furthermore, the suction pressure of the suction nozzle 32 was set to 1100 Pa.
[0137] Experiment 3... is th...
PUM
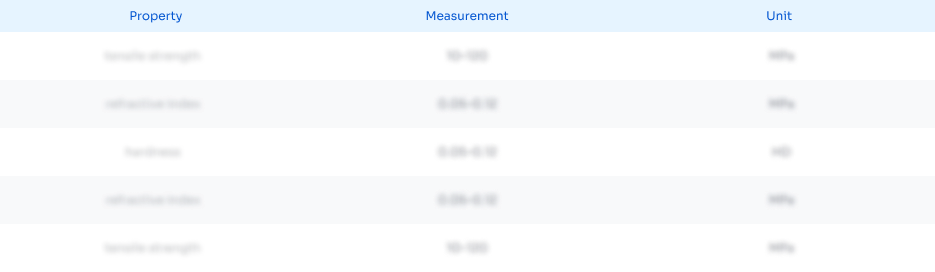
Abstract
Description
Claims
Application Information

- R&D Engineer
- R&D Manager
- IP Professional
- Industry Leading Data Capabilities
- Powerful AI technology
- Patent DNA Extraction
Browse by: Latest US Patents, China's latest patents, Technical Efficacy Thesaurus, Application Domain, Technology Topic.
© 2024 PatSnap. All rights reserved.Legal|Privacy policy|Modern Slavery Act Transparency Statement|Sitemap