Process for producing methyl hydrazine with hydrazine hydrate method
A technology of hydrazine hydrate and methyl hydrazine, applied in the fields of hydrazine preparation, organic chemistry, etc., can solve the problems of poor product quality, high energy consumption, high pollution, etc., to reduce the cost of three wastes treatment, reduce the consumption of raw materials, and improve the safety factor. Effect
- Summary
- Abstract
- Description
- Claims
- Application Information
AI Technical Summary
Problems solved by technology
Method used
Image
Examples
Embodiment 1
[0024] Such as figure 1 As shown, the process of producing methylhydrazine by the hydrazine hydrate method of the present invention comprises the following steps: first put 480 parts by mass of hydrazine hydrate with a concentration of 75% into the salt-forming kettle, start stirring, control the temperature to 20°C, and then dropwise add 1051 parts by mass of hydrochloric acid with a concentration of 25%, adjust the pH to 6.5-7.0, after the reaction is completed, heat the temperature to 70°C, carry out dehydration under reduced pressure, and control the pressure to -0.1Mpa to obtain hydrazine hydrochloride; use the obtained hydrazine hydrochloride as a catalyst Transfer to the methylation reaction kettle, then add 900 parts by mass of methanol with a concentration of 95%, then seal the methylation reaction kettle, heat up to 90°C to carry out the methylation reaction, control the reaction pressure to 0.5MPa, react for 2h, and react After the end, the temperature was lowe...
Embodiment 2
[0027] Such as figure 1 As shown, the process for producing methylhydrazine by the hydrazine hydrate method of the present invention comprises the following steps: first put 500 parts by mass of hydrazine hydrate with a concentration of 75% into the salt-forming kettle, start stirring, control the temperature to 30°C, and then dropwise add 912 parts by mass of hydrochloric acid with a concentration of 30%, adjust the pH to be 6.5-7.0, after the reaction is completed, heat the temperature to 80°C, carry out dehydration under reduced pressure, and control the pressure to be -0.1Mpa to obtain hydrazine hydrochloride; the obtained hydrazine hydrochloride is transferred to Add 920 parts by mass of methanol with a concentration of 96% to the methylation reaction kettle, then seal the methylation reaction kettle, raise the temperature to 105°C for the methylation reaction, control the reaction pressure to 0.6MPa, react for 2.5h, and the reaction ends After that, the temperature w...
Embodiment 3
[0029] Such as figure 1 Shown, the technique that hydrazine hydrate method of the present invention produces methylhydrazine comprises the steps:
[0030] First put 520 parts by mass of hydrazine hydrate with a concentration of 80% into the salt-forming kettle, start stirring, control the temperature at 40°C, then add 1012 parts by mass of hydrochloric acid with a concentration of 30% dropwise, adjust the pH to 6.5-7.0, and the reaction is complete Finally, heat the temperature to 90°C, carry out dehydration under reduced pressure, and control the pressure to -0.1Mpa to obtain hydrazine hydrochloride; transfer the obtained hydrazine hydrochloride into a methylation reaction kettle, and then add 950 parts by mass of methanol with a concentration of 98%. Then close the methylation reaction kettle, raise the temperature to 120°C for methylation reaction, control the reaction pressure to 0.7MPa, react for 3 hours, after the reaction is completed, cool down to 55°C, put it into the...
PUM
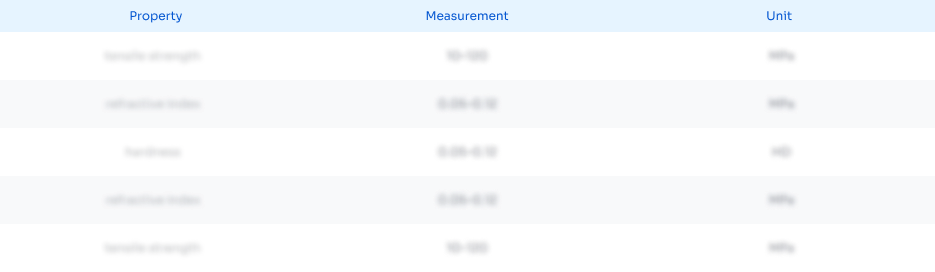
Abstract
Description
Claims
Application Information

- Generate Ideas
- Intellectual Property
- Life Sciences
- Materials
- Tech Scout
- Unparalleled Data Quality
- Higher Quality Content
- 60% Fewer Hallucinations
Browse by: Latest US Patents, China's latest patents, Technical Efficacy Thesaurus, Application Domain, Technology Topic, Popular Technical Reports.
© 2025 PatSnap. All rights reserved.Legal|Privacy policy|Modern Slavery Act Transparency Statement|Sitemap|About US| Contact US: help@patsnap.com