Method for setting flow of hot rolling cooling system
A technology of flow setting and cooling system, applied in the direction of temperature control, etc., to improve the hit rate of the strip and the uniformity of the strip performance, achieve fine control, and solve the effect of uneven cooling
- Summary
- Abstract
- Description
- Claims
- Application Information
AI Technical Summary
Problems solved by technology
Method used
Image
Examples
specific Embodiment approach
[0014] see figure 1 , the specific embodiment of the present invention is as follows:
[0015] First, set the pressure condition of the header according to the process, and construct the proportional segmental function of flow rate and header opening: flow = k × header opening + b, where k and b are the required flow rate and actuator performance parameters according to the process determined constant.
[0016] Then, according to the process set pressure and the set medium flow rate, the linear interpolation method is used to compare and interpolate the node medium flow rate under the process set pressure condition, and determine the function of the node interval corresponding to the process set flow rate;
[0017] According to the preset flow value, the opening degree of the header is obtained through the function determined above, and the control parameters required for the opening degree of the header are sent to the actuator for execution—the flow regulating valve.
[00...
PUM
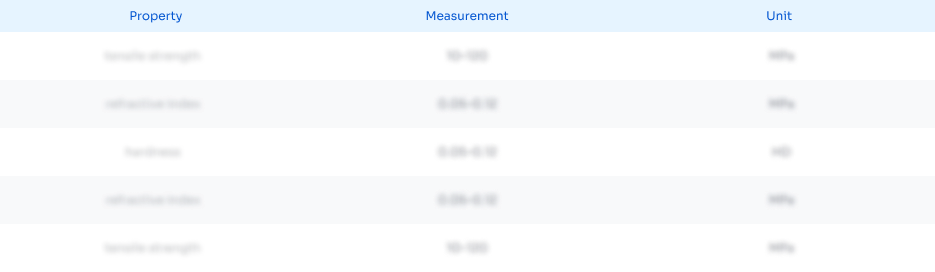
Abstract
Description
Claims
Application Information

- Generate Ideas
- Intellectual Property
- Life Sciences
- Materials
- Tech Scout
- Unparalleled Data Quality
- Higher Quality Content
- 60% Fewer Hallucinations
Browse by: Latest US Patents, China's latest patents, Technical Efficacy Thesaurus, Application Domain, Technology Topic, Popular Technical Reports.
© 2025 PatSnap. All rights reserved.Legal|Privacy policy|Modern Slavery Act Transparency Statement|Sitemap|About US| Contact US: help@patsnap.com