Wind driven permanent magnetic ore dressing method
A mineral processing method and permanent magnet technology, applied in chemical instruments and methods, magnetic separation, solid separation, etc., can solve problems such as potential safety hazards, prone to landslides, serious water and power consumption, etc., to prevent landslides and solve environmental pollution problems , the effect of saving water resources
- Summary
- Abstract
- Description
- Claims
- Application Information
AI Technical Summary
Problems solved by technology
Method used
Image
Examples
Embodiment Construction
[0021] The specific implementation manner of the present invention will be described below in conjunction with the accompanying drawings.
[0022] Such as figure 1 The shown wind-force permanent magnet dry-type mineral processing method comprises the following steps:
[0023] Step 1. Use the crocodile crusher to crush the mined raw ore, and break the large ore of different sizes into small ore of the same size to form coarse ore;
[0024] Step 2. Transport the coarse ore to the double-stage hammer crusher through the conveyor belt for further crushing, and crush the coarse ore to a size of less than 3mm (that is, the length, width and height of the ore are all less than 3mm) to form fine ore;
[0025] Step 3. The fine ore is transported to the cylindrical screening device through the conveying device, and the fine ore above 3 mm is screened out and returned to step 2 for further processing. A moisture measuring instrument is installed in the screening device, and the moisture...
PUM
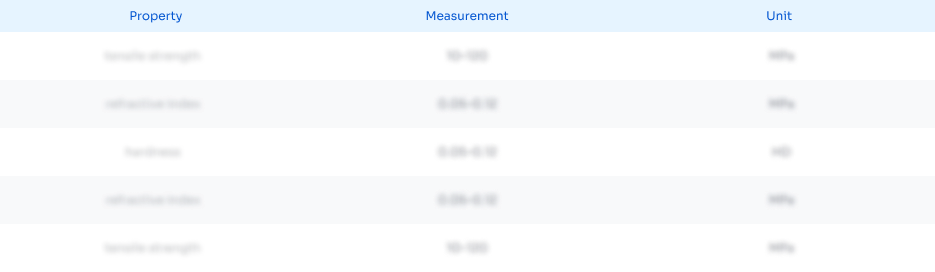
Abstract
Description
Claims
Application Information

- Generate Ideas
- Intellectual Property
- Life Sciences
- Materials
- Tech Scout
- Unparalleled Data Quality
- Higher Quality Content
- 60% Fewer Hallucinations
Browse by: Latest US Patents, China's latest patents, Technical Efficacy Thesaurus, Application Domain, Technology Topic, Popular Technical Reports.
© 2025 PatSnap. All rights reserved.Legal|Privacy policy|Modern Slavery Act Transparency Statement|Sitemap|About US| Contact US: help@patsnap.com