Method for manufacturing quill roller for bearing
A manufacturing method and needle roller technology, applied in the field of mechanical parts processing, can solve the problems of low processing efficiency of needle rollers and short service life of needle rollers, and achieve the effects of preventing uneven grinding, improving production efficiency and high contact fatigue performance.
- Summary
- Abstract
- Description
- Claims
- Application Information
AI Technical Summary
Problems solved by technology
Method used
Examples
Embodiment 1
[0024] Select GCr15 steel to form a needle blank after cutting, and then use a barrel polisher to roll and polish the two ends of the needle into a spherical surface (throwing R balls). The barrel polisher can process 200kg of needles in each batch. The number of revolutions of the barrel polisher is 350 rpm, and the running time of the barrel polisher is 48 hours.
[0025] Then the needle roller blank after rolling and polishing is ground successively on a centerless grinder and a barrel polishing machine to remove the burrs on the surface of the needle roller and the peripheral spherical surface at both ends of the needle roller (throwing R angle).
[0026] Put it in a continuous furnace for heat treatment, heat treatment includes quenching step and tempering step, quenching step: temperature is 850 ° C, holding time is 170 minutes, HRC hardness is 66; during the quenching step, methanol is used for gas protection, and the flow rate of methanol 2L / h; tempering steps: tempera...
Embodiment 2
[0028] Select GCr15 steel to form a needle blank after cutting, and then use a barrel polisher to roll and polish the two ends of the needle into a spherical surface (throwing R balls). The barrel polisher can handle 280kg of needles per batch. The number of revolutions of the barrel polisher is 330 rpm, and the running time of the barrel polisher is 50 hours.
[0029] Then the needle roller blank after rolling and polishing is ground successively on a centerless grinder and a barrel polishing machine to remove the burrs on the surface of the needle roller and the peripheral spherical surface at both ends of the needle roller (throwing R angle).
[0030] Then it is placed in a continuous furnace for heat treatment, which includes a quenching step and a tempering step. Quenching step: the temperature is 830° C., the holding time is 190 minutes, and the HRC hardness is 64; methanol is used for gas protection during the quenching step, and the flow rate of methanol is 4 L / h. Tem...
Embodiment 3
[0032] Select GCr15 steel to form a needle blank after cutting, and then use a barrel polishing machine to roll and polish both ends of the needle into a spherical surface (throwing R balls). The barrel polishing machine can process 250kg of needles in each batch. The number of revolutions of the barrel polisher was 320 rpm, and the running time of the barrel polisher was 49 hours.
[0033] Then the needle roller blank after rolling and polishing is ground successively on a centerless grinder and a barrel polishing machine to remove the burrs on the surface of the needle roller and the peripheral spherical surface at both ends of the needle roller (throwing R angle).
[0034] Then it is placed in a continuous furnace for heat treatment, which includes a quenching step and a tempering step. Quenching step: the temperature is 880° C., the holding time is 240 minutes, and the HRC hardness is 68; methanol is used for gas protection during the quenching step, and the flow rate of m...
PUM
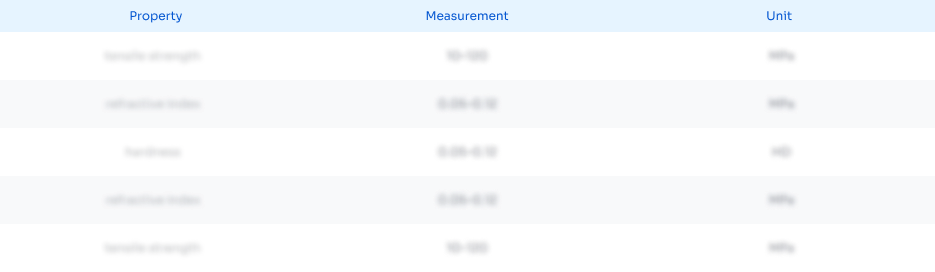
Abstract
Description
Claims
Application Information

- R&D
- Intellectual Property
- Life Sciences
- Materials
- Tech Scout
- Unparalleled Data Quality
- Higher Quality Content
- 60% Fewer Hallucinations
Browse by: Latest US Patents, China's latest patents, Technical Efficacy Thesaurus, Application Domain, Technology Topic, Popular Technical Reports.
© 2025 PatSnap. All rights reserved.Legal|Privacy policy|Modern Slavery Act Transparency Statement|Sitemap|About US| Contact US: help@patsnap.com