Method for monitoring intra-furnace dynamic wall temperature in high-temperature tube system of power station boiler
A technology for power station boilers and high-temperature tubes, which is applied to the indication of boiler working conditions, thermometer components, temperature measurement of moving fluids, etc. It is difficult to obtain the instrument, lack of modeling basis, accuracy and reliability, etc.
- Summary
- Abstract
- Description
- Claims
- Application Information
AI Technical Summary
Problems solved by technology
Method used
Image
Examples
Embodiment
[0127] In this example, a 1000MW ultra-supercritical boiler in a power plant is selected, and the high-temperature reheater piping system adopts figure 1 The block schematic diagram of the implementation steps is shown.
[0128] This embodiment includes the following steps:
[0129] Step 1: Through pre-calculation, it is obtained that the typical temperature margin of the inner wall of the furnace in the piping system of the high-temperature reheater of the 1000MW ultra-supercritical boiler is installed to measure and collect the temperature of the outer wall of the furnace.
[0130] The high-temperature reheater of the 1000MW ultra-supercritical boiler has a total of 44 screens, and each screen has 24 tubes. A total of 1056 pipes are used to calculate 6336 pipe sections.
[0131] a. Calculate the enthalpy increase Δia of the pipe section
[0132] Δia=Kry(Q d +Q p +Q q +Q qq +Q z +Q h +Q x ) / ga
[0133] Where: Kr y The width endothermic deviation coefficient set fo...
PUM
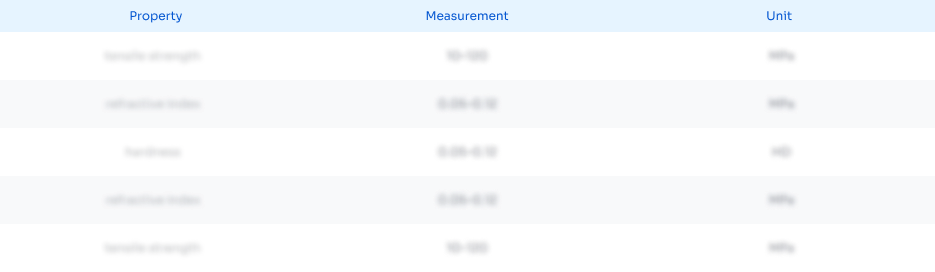
Abstract
Description
Claims
Application Information

- Generate Ideas
- Intellectual Property
- Life Sciences
- Materials
- Tech Scout
- Unparalleled Data Quality
- Higher Quality Content
- 60% Fewer Hallucinations
Browse by: Latest US Patents, China's latest patents, Technical Efficacy Thesaurus, Application Domain, Technology Topic, Popular Technical Reports.
© 2025 PatSnap. All rights reserved.Legal|Privacy policy|Modern Slavery Act Transparency Statement|Sitemap|About US| Contact US: help@patsnap.com