Slewing system for hybrid hydraulic excavator and driving and braking method for slewing system
A technology of hybrid power and slewing system, applied in the direction of earth mover/shovel, construction, etc., can solve the problem of low energy recovery efficiency, and achieve the effect of improving efficiency, improving reliability and easy realization.
- Summary
- Abstract
- Description
- Claims
- Application Information
AI Technical Summary
Problems solved by technology
Method used
Image
Examples
specific Embodiment approach 1
[0019] Specific implementation mode one: the following combination figure 1 Describe this embodiment. The hydraulic hybrid excavator slewing system described in this embodiment includes a variable pump 1 and a multi-way valve 2. It also includes an electric proportional throttle valve 3, a one-way valve 4, an electronically controlled on-off valve 5, The first manual reversing valve 6, the second manual reversing valve 7, the relief valve 8, the hydraulic pump / motor 9, the hydraulic accumulator 10, the pressure sensor 11 and the controller 12,
[0020] The oil inlet port of the multi-way valve 2 is connected with the high-pressure oil port of the variable pump 1, the A port of the multi-way valve 2 is connected with the d port of the second manual reversing valve 7, and the B port of the multi-way valve 2 is connected with the second manual reversing valve Port c of 7, port b of the second manual reversing valve 7 is connected to the low-pressure oil port of the hydraulic pump...
specific Embodiment approach 2
[0024] Specific implementation mode two: the following combination figure 1 Describe this embodiment. This embodiment is based on the driving and braking method of the hydraulic hybrid excavator swing system described in Embodiment 1. The swing system in this embodiment replaces the motor in the existing swing system with a hydraulic pump / motor. 9. After installing other related components, switch the working mode through the switching of two manual reversing valves.
[0025] The slewing system described in the present invention has two working modes in actual work:
[0026] The first type: hybrid power mode, which adopts the slewing system described in the present invention to realize driving and braking. The first manual reversing valve 6 is adjusted to the upper position and the second manual reversing valve 7 is adjusted to the neutral position. The slewing system is put into a hybrid power mode with the function of recovering energy. This mode utilizes the feature that t...
PUM
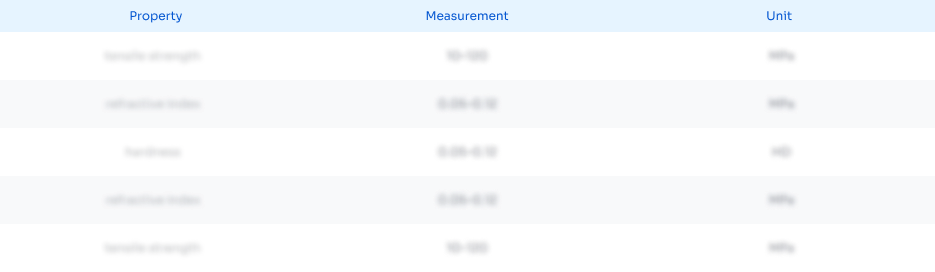
Abstract
Description
Claims
Application Information

- R&D
- Intellectual Property
- Life Sciences
- Materials
- Tech Scout
- Unparalleled Data Quality
- Higher Quality Content
- 60% Fewer Hallucinations
Browse by: Latest US Patents, China's latest patents, Technical Efficacy Thesaurus, Application Domain, Technology Topic, Popular Technical Reports.
© 2025 PatSnap. All rights reserved.Legal|Privacy policy|Modern Slavery Act Transparency Statement|Sitemap|About US| Contact US: help@patsnap.com