Cooling method for hot-rolled sheet steel
A technology of hot-rolled steel sheet and cooling method, applied in workpiece cooling device, driving device for metal rolling mill, metal rolling, etc., to achieve the effect of suppressing uneven cooling, suppressing deviation, and suppressing the temperature of coiled steel plate
- Summary
- Abstract
- Description
- Claims
- Application Information
AI Technical Summary
Problems solved by technology
Method used
Image
Examples
Embodiment
[0076] Hereinafter, Examples A1 to A7, Examples B1 to B7, Examples C1 to C7, and Examples D1 to D7 performed using the finish rolling mill, the first cooler, the second cooler, and the coiler will be described.
[0077] In various embodiments, based on Figure 7 In the transfer speed change schedule shown, the finish rolling of the hot-rolled steel sheet was performed, and then the first cooling and the second cooling were performed. Table 1 shows respective cooling conditions and evaluation results. exist Figure 7 Among them, t=0 is the time when the front end of the hot-rolled steel sheet reaches the first cooling zone, and t=90 is the time when the rear end of the hot-rolled steel sheet reaches the coiler. In this example, evaluation was performed by setting the conveyance speed at t=20 as the first conveyance speed and the conveyance speed at t=50 as the second conveyance speed. In addition, the outlet-side target steel plate temperature in the second cooling section w...
PUM
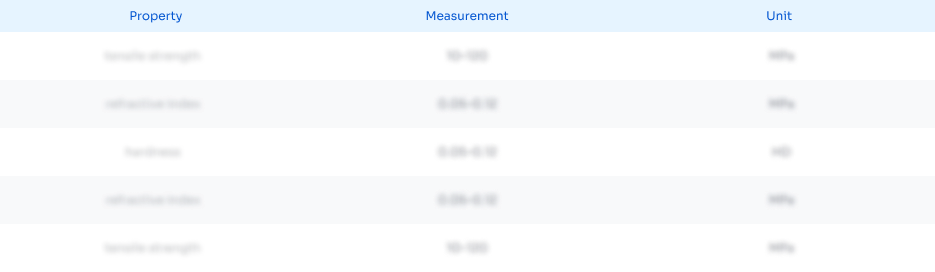
Abstract
Description
Claims
Application Information

- R&D Engineer
- R&D Manager
- IP Professional
- Industry Leading Data Capabilities
- Powerful AI technology
- Patent DNA Extraction
Browse by: Latest US Patents, China's latest patents, Technical Efficacy Thesaurus, Application Domain, Technology Topic, Popular Technical Reports.
© 2024 PatSnap. All rights reserved.Legal|Privacy policy|Modern Slavery Act Transparency Statement|Sitemap|About US| Contact US: help@patsnap.com