Sulfur recovery plant tail gas treatment process
A tail gas and gas flow technology, applied in the direction of gas treatment, separation methods, chemical instruments and methods, etc., to achieve the effect of reducing investment costs and minimizing capital requirements
- Summary
- Abstract
- Description
- Claims
- Application Information
AI Technical Summary
Problems solved by technology
Method used
Image
Examples
Embodiment Construction
[0022] Exhaust gas treatment device
[0023] This figure illustrates an exemplary configuration for the exhaust gas treatment method of the present invention. The off-gas from the two- or three-stage Claus unit enters the unit via line 10 . At this point, in a conventional BSR or SCOT unit, the tail gas will be sent to a reducing gas generator (RGG), where hydrogen is produced by substoichiometric combustion of natural gas for almost all non-H 2Catalytic reduction of S sulfur components. Passing the Claus tail gas through the RGG typically heats the gas to a temperature of 290-340°C. Alternatively, an exhaust gas preheater can be used to heat the exhaust gas and add H 2 The stream is used for the hydrogenation reaction. SO in the hydrogenation reactor 2 and elemental sulfur are converted by hydrogenation, while CO, COS and CS 2 is hydrolyzed to CO 2 , convert any CO produced into CO by the water-gas shift reaction 2 . This heated gas mixture then enters a conventional...
PUM
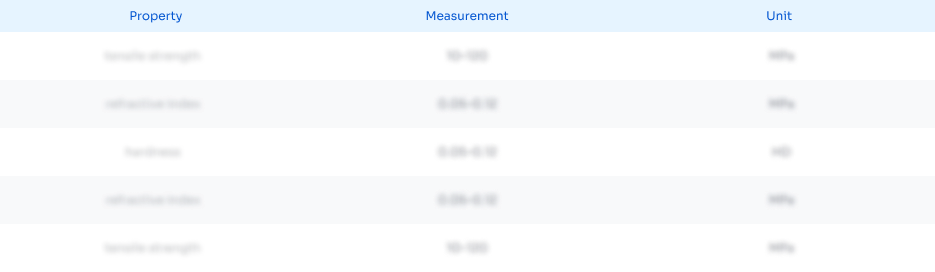
Abstract
Description
Claims
Application Information

- R&D Engineer
- R&D Manager
- IP Professional
- Industry Leading Data Capabilities
- Powerful AI technology
- Patent DNA Extraction
Browse by: Latest US Patents, China's latest patents, Technical Efficacy Thesaurus, Application Domain, Technology Topic, Popular Technical Reports.
© 2024 PatSnap. All rights reserved.Legal|Privacy policy|Modern Slavery Act Transparency Statement|Sitemap|About US| Contact US: help@patsnap.com