Process for manufacturing kapok fiber blended yarns
A kapok fiber and manufacturing process technology, applied in the field of multi-fiber blended yarn manufacturing technology, can solve the problems of difficult kapok fiber blended yarn and efficiency, low yarn breaking strength, fine kapok fiber count, etc., and achieve excellent evenness and strength, less yarn breakage and better yarn quality
- Summary
- Abstract
- Description
- Claims
- Application Information
AI Technical Summary
Problems solved by technology
Method used
Image
Examples
Embodiment Construction
[0017] The product of the present invention is a blended yarn of selected high-quality kapok fiber and cotton fiber, wool, silk, hemp fiber and polyester fiber, wherein the content of kapok fiber accounts for 25%-60% of the total weight of the blended yarn described in the present invention , the content of cotton fiber, wool, silk, hemp fiber and polyester fiber accounts for 40%-75% of the total weight of the blended yarn in the present invention. When the kapok fiber content is lower, it is easier to blend with other fibers, but the lower the kapok content, the blended yarn will not reflect the softness of the kapok fiber, and its fabric will not be able to reflect the advantages of the kapok fiber itself. Therefore, in the present invention The minimum limit of kapok fiber content control is 25%. When the kapok fiber content is higher, the corresponding manufacturing cost is higher and the difficulty is greater. When it is higher than a certain range, it will also bring con...
PUM
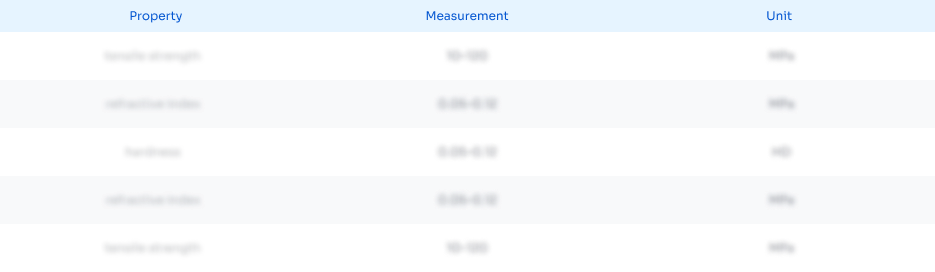
Abstract
Description
Claims
Application Information

- R&D
- Intellectual Property
- Life Sciences
- Materials
- Tech Scout
- Unparalleled Data Quality
- Higher Quality Content
- 60% Fewer Hallucinations
Browse by: Latest US Patents, China's latest patents, Technical Efficacy Thesaurus, Application Domain, Technology Topic, Popular Technical Reports.
© 2025 PatSnap. All rights reserved.Legal|Privacy policy|Modern Slavery Act Transparency Statement|Sitemap|About US| Contact US: help@patsnap.com