Built-in main fixture
A technology with built-in main fixtures and fixtures, applied in auxiliary devices, manufacturing tools, auxiliary welding equipment, etc., can solve the problems of poor size control of the lower part of the car body, no self-locking function, and large floor area of the main assembly station, etc., to achieve reduction Cost and cycle, smooth and fast lifting, and the effect of ensuring dimensional accuracy
- Summary
- Abstract
- Description
- Claims
- Application Information
AI Technical Summary
Problems solved by technology
Method used
Image
Examples
Embodiment Construction
[0026] Below in conjunction with accompanying drawing, the present invention will be further described: as figure 1 As shown, the built-in main fixture is composed of the lower body positioning fixture 3, the built-in fixture body 2, the lifting mechanism 4, and the switching system 1; it is characterized in that a four-point positioning method is adopted between the built-in fixture body 2 and the lower body fixture 3, and four The center of the positioning point is located at the center of gravity of the built-in fixture body 2 to ensure that the positioning error is eliminated to the greatest extent during the positioning process; two circular check pins and two diamond-shaped check pins are arranged at the four positioning points, and the built-in fixture body 2 is lowered It plays a guiding role in the process and eliminates the position deviation generated during the descent. When the built-in fixture body 2 falls in place, the positioning hole 2-1 on the built-in fixtur...
PUM
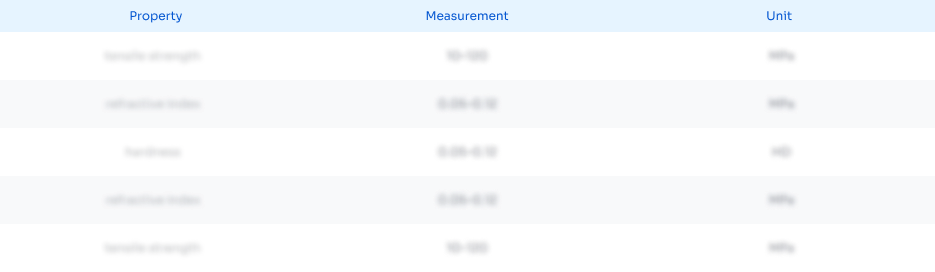
Abstract
Description
Claims
Application Information

- R&D
- Intellectual Property
- Life Sciences
- Materials
- Tech Scout
- Unparalleled Data Quality
- Higher Quality Content
- 60% Fewer Hallucinations
Browse by: Latest US Patents, China's latest patents, Technical Efficacy Thesaurus, Application Domain, Technology Topic, Popular Technical Reports.
© 2025 PatSnap. All rights reserved.Legal|Privacy policy|Modern Slavery Act Transparency Statement|Sitemap|About US| Contact US: help@patsnap.com