Hydraulic differential pilot opening mechanism
An opening mechanism and differential technology, applied in the field of hydraulic components, can solve the problems of easy vibration and howling of the pilot valve core, large impact of the pilot valve, and short life.
- Summary
- Abstract
- Description
- Claims
- Application Information
AI Technical Summary
Problems solved by technology
Method used
Image
Examples
Embodiment 1
[0025] Such as figure 2As shown, the hydraulic differential pilot opening mechanism includes a valve body 1 and a bonnet 9 screwed to the valve body. A pilot valve cavity is formed in the valve body and the bonnet, and a pilot valve is slidably arranged in the pilot valve cavity. The inner side is the first cavity 3, the valve body 1 is provided with an oil inlet 12 communicating with the first cavity 3, the second cavity 6 is provided on the outside of the pilot valve, and the pilot valve core 4 is provided with a connection with the first cavity 3 and the orifice 13 of the second cavity 6, such as image 3 As shown, the pilot valve includes a pilot valve core 4 and a pilot valve seat 5, and the pilot valve seat 5 is in sliding fit with the inner wall of the pilot valve cavity. It includes a guide portion 18 at the head, a sealing cone 14 at the tail, and a connecting portion 15 connecting the guiding portion and the sealing cone. The sealing cone 14 is located in the first...
Embodiment 2
[0028] Such as Figure 5 As shown, compared with the first embodiment, the difference is that: the outer side of the pilot valve seat 5 has a cylindrical concave cavity, and the side wall of the concave cavity is slidingly fitted with the side wall of the limit post 8, and the pilot valve seat 5 The second cavity 6 is formed with the limiting post 8 , and a second sealing groove 26 is provided on the side of the limiting post 8 cooperating with the pilot valve seat 5 , and a second sealing ring 27 is embedded in the second sealing groove. The bonnet 9 is provided with a fixed cap 24, and the center of the fixed cap is provided with a limit post fixing hole 25. The limit post is inserted in the fixed hole 25, and is fixedly connected with the fixed cap by tight fit or screw threads. The side surface is connected with the inner surface of the bonnet 9, the pressure regulating spring 7 is in contact with the fixed cap, and a pressure regulating gasket 10 is arranged between the t...
Embodiment 3
[0030] Such as Image 6 As shown, compared with the first embodiment, the difference is that a sealing sleeve 29 is provided on the outside of the small diameter section of the pilot valve seat 5, and the inner side wall of the sealing sleeve 29 is in contact with the outer side wall of the small diameter section of the pilot valve seat 5. Slip fit, the two ends of the sealing sleeve 29 are in contact with the valve body 1 and the bonnet 9 respectively, and are axially positioned by the extrusion of the bonnet 9 . In this embodiment, by providing the sealing sleeve 29, the coaxiality requirement between the sealing sleeve 29 and the pilot valve seat 5 can be easily met during the manufacturing process, which can reduce the difficulty of manufacturing.
PUM
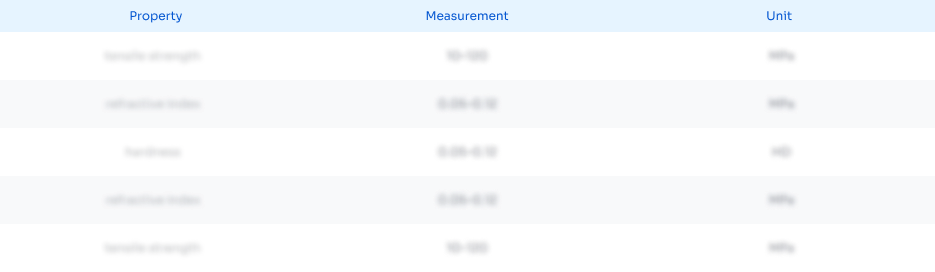
Abstract
Description
Claims
Application Information

- R&D
- Intellectual Property
- Life Sciences
- Materials
- Tech Scout
- Unparalleled Data Quality
- Higher Quality Content
- 60% Fewer Hallucinations
Browse by: Latest US Patents, China's latest patents, Technical Efficacy Thesaurus, Application Domain, Technology Topic, Popular Technical Reports.
© 2025 PatSnap. All rights reserved.Legal|Privacy policy|Modern Slavery Act Transparency Statement|Sitemap|About US| Contact US: help@patsnap.com