Boom element, telescopic boom and construction vehicle
A telescopic boom technology, which is applied in telescopic joints or telescopic boom hinges, engineering vehicles, and telescopic booms, can solve problems such as boom weight, reduce production costs, ensure quality, and lighten the structure. Effect
- Summary
- Abstract
- Description
- Claims
- Application Information
AI Technical Summary
Problems solved by technology
Method used
Image
Examples
Embodiment Construction
[0053] figure 1 A schematic front view of a part of a telescopic boom according to the invention is shown, wherein here two telescopic joints 1 and 2 are shown. as can be obtained from figure 1 As seen in the figure, a shell-shaped corner rod 20 is used in each telescopic joint 1, 2, 3, 4.
[0054] The corner bar 20 can be produced as folded, bent, from a tubular section or even from an extruded profile. The corner bars 20 are connected by truss bars 21 which are at right angles to the corner bars 20 (called zero bars) or / and also at another angle to the corner bars 20 (called diagonal bars) ground layout.
[0055] Each truss bar 21 can also be made of a welded structure consisting of four plates, as figure 2 as shown in . figure 2 shows from figure 1 Sectional view A-A. The resistance moment Wx about the X-axis x is as large as the resistance moment Wy about the Y-axis y and corresponds to a circular pipe section. A tubular lattice bar 21 is thus simulated and a "fl...
PUM
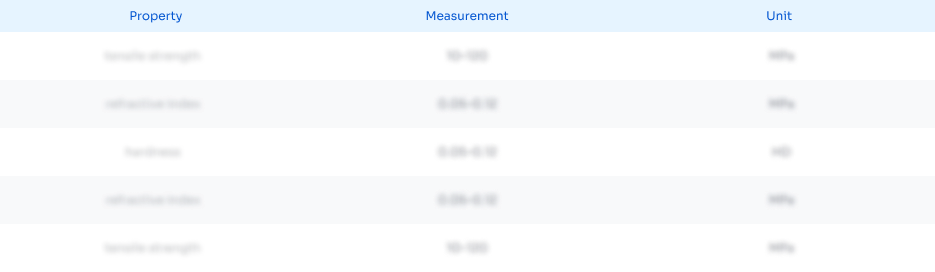
Abstract
Description
Claims
Application Information

- Generate Ideas
- Intellectual Property
- Life Sciences
- Materials
- Tech Scout
- Unparalleled Data Quality
- Higher Quality Content
- 60% Fewer Hallucinations
Browse by: Latest US Patents, China's latest patents, Technical Efficacy Thesaurus, Application Domain, Technology Topic, Popular Technical Reports.
© 2025 PatSnap. All rights reserved.Legal|Privacy policy|Modern Slavery Act Transparency Statement|Sitemap|About US| Contact US: help@patsnap.com