Optical film processing die and manufacturing method thereof
A technology for processing molds and manufacturing methods, which is applied in the direction of plating of superimposed layers, metal material coating technology, coating, etc., can solve the defects that affect the surface shape of the diaphragm, the appearance of the optical diaphragm, and reduce the adhesion between UV glue and the substrate. Focus on issues such as improving life, preventing optical film defects, and preventing optical defects
- Summary
- Abstract
- Description
- Claims
- Application Information
AI Technical Summary
Problems solved by technology
Method used
Image
Examples
Embodiment Construction
[0018] The optical film processing mold provided by the technical solution and the manufacturing method thereof will be further described in detail below in conjunction with the accompanying drawings.
[0019] see figure 1 flow chart and see also figure 2 The first embodiment of the technical solution provides a method for manufacturing an optical film processing mold 10. The method includes the following steps: (1). Provide a mold base 12 with a copper surface 120; (2). The copper surface 120 of the mold base 12 is oxidized to form a layer of copper oxide film 14 on the copper surface 120 of the mold base 12; (3). A layer of copper oxide film 14 is formed by the reaction of fluorinated fatty acid with the copper oxide film 14 Fluorinating the self-assembled monomolecular film layer 16; (4). Cleaning the fluorinated self-assembled monomolecular film layer 16.
[0020] The mold base 12 provided in step (1) with a copper surface 120 can be a copper roller, of course, the mold...
PUM
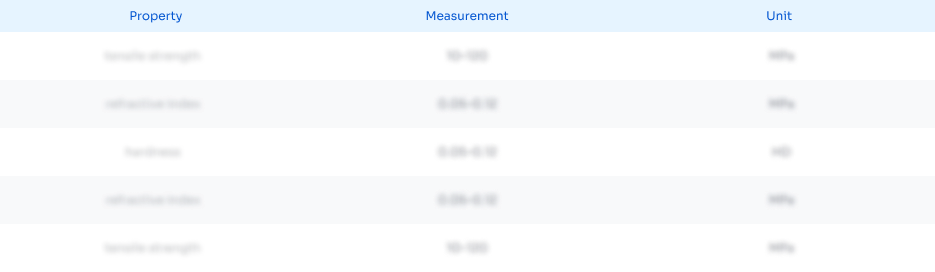
Abstract
Description
Claims
Application Information

- Generate Ideas
- Intellectual Property
- Life Sciences
- Materials
- Tech Scout
- Unparalleled Data Quality
- Higher Quality Content
- 60% Fewer Hallucinations
Browse by: Latest US Patents, China's latest patents, Technical Efficacy Thesaurus, Application Domain, Technology Topic, Popular Technical Reports.
© 2025 PatSnap. All rights reserved.Legal|Privacy policy|Modern Slavery Act Transparency Statement|Sitemap|About US| Contact US: help@patsnap.com