Spectral plane or focal plane installation and debugging method of hyperspectral imager
An installation and adjustment method and imager technology, which are applied in spectrum investigation and other directions, can solve the problems of position adjustment of CCD focal plane components, damage of CCD devices, complicated installation and adjustment process, etc., and achieve the effect of simple installation and adjustment process.
- Summary
- Abstract
- Description
- Claims
- Application Information
AI Technical Summary
Problems solved by technology
Method used
Image
Examples
specific Embodiment approach 1
[0017] Specific implementation mode 1. Combination Figure 1 to Figure 6 To describe this embodiment,
[0018] First, the focal plane adjustment module 5 is according to the distance Ht=H, Xt=X, Yt=Y from the reference mounting surface of the CCD focal plane assembly 6 to the image plane of the hyperspectral imager 7, and Xt, Yt, and Ht are the focal plane mounting planes respectively. The length, width and height of the adjustment module 5, X, Y, and H are the length, width and height of the CCD focal plane assembly 6 respectively, and the position of the focal plane adjustment module 5 to the image plane of the hyperspectral imager 7 is in line with the CCD focal plane. The corresponding adjustment of the position of the surface assembly 6 to the position of the image plane of the hyperspectral imager 7; Image 6 , the CCD photosensitive surface 12 on the CCD focal plane assembly 6 coincides with the spectral surface of the hyperspectral imager 7, that is, the position of t...
PUM
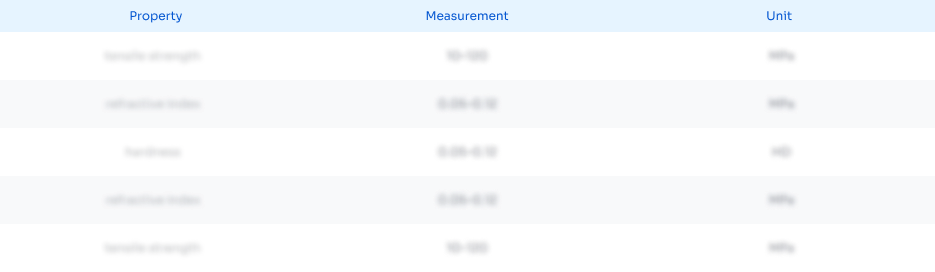
Abstract
Description
Claims
Application Information

- Generate Ideas
- Intellectual Property
- Life Sciences
- Materials
- Tech Scout
- Unparalleled Data Quality
- Higher Quality Content
- 60% Fewer Hallucinations
Browse by: Latest US Patents, China's latest patents, Technical Efficacy Thesaurus, Application Domain, Technology Topic, Popular Technical Reports.
© 2025 PatSnap. All rights reserved.Legal|Privacy policy|Modern Slavery Act Transparency Statement|Sitemap|About US| Contact US: help@patsnap.com