Production method of automobile skylight slide plate made of paper honeycomb-shape core material
A technology of automobile sunroof and production method, which is applied in the field of automobile interior parts, can solve the problems such as the heavy weight of the sunroof slide plate, and achieve the effects of reducing the weight of the car, environmental protection, weather resistance, and high rigidity
- Summary
- Abstract
- Description
- Claims
- Application Information
AI Technical Summary
Problems solved by technology
Method used
Examples
Embodiment 1
[0019] Fiat 343 sunroof skateboard, its specification is: L564.5×W774mm.
[0020] Including the following production process steps:
[0021] (1) Material placement: Lay the materials on the workbench in the order of glass fiber, paper honeycomb core material, and glass fiber;
[0022] (2) Polyurethane spraying: Fix the paved material on the manipulator, send it to the spraying room for AB material spraying until the material is fully infiltrated;
[0023] (3) Compression molding: Place the infiltrated material in a molding machine for positioning, molding, and punching to obtain a molding material; the molding temperature of the upper mold of the mold is 120°C, the molding temperature of the lower mold is 125°C, and the molding pressure is 7.5MPa. Time: 130s;
[0024] (4) Cooling and shaping: Take the molding material out of the mold, put it on the cooling fixture for cooling and shaping at room temperature, the cooling time is 45s, after cooling and shaping, remove the surr...
Embodiment 2
[0031] 353 sunroof slide plate, its specification is: L1120×W850mm.
[0032] Including the following production process steps:
[0033] (1) Material placement: Lay the materials on the workbench in the order of glass fiber, paper honeycomb core material, and glass fiber;
[0034] (2) Polyurethane spraying: Fix the paved material on the manipulator, send it to the spraying room for AB material spraying until the material is fully infiltrated;
[0035] (3) Compression molding: Place the infiltrated material in a molding machine for positioning, forming and punching to obtain a molding material; the molding temperature of the upper mold of the mold is 130°C, the molding temperature of the lower mold is 145°C, and the molding pressure is 8.5MPa. Time: 140s;
[0036] (4) Cooling and shaping: Take the molding material out of the mold, put it on the cooling fixture for cooling and shaping at room temperature, the cooling time is 50s, after cooling and shaping, remove the surroundin...
Embodiment 3
[0043] 464 sunroof slide plate, its specification is: L1100×W820mm.
[0044] Including the following production process steps:
[0045] (1) Material placement: Lay the materials on the workbench in the order of glass fiber, paper honeycomb core material, and glass fiber;
[0046] (2) Polyurethane spraying: Fix the paved material on the manipulator, send it to the spraying room for AB material spraying until the material is fully infiltrated;
[0047] (3) Compression molding: place the infiltrated material in a molding machine for positioning, forming and punching to obtain a molding material; the molding temperature of the upper mold of the mold is 120°C, the molding temperature of the lower mold is 135°C, the molding pressure is 8MPa, and the molding time : 130s;
[0048] (4) Cooling and shaping: Take the molding material out of the mold, put it on the cooling fixture for cooling and shaping at room temperature, the cooling time is 50s, after cooling and shaping, remove the...
PUM
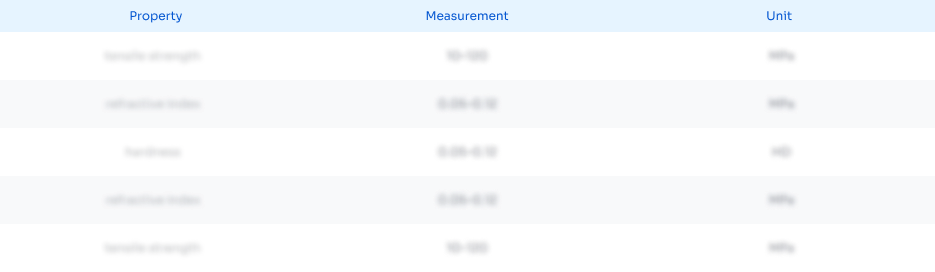
Abstract
Description
Claims
Application Information

- R&D Engineer
- R&D Manager
- IP Professional
- Industry Leading Data Capabilities
- Powerful AI technology
- Patent DNA Extraction
Browse by: Latest US Patents, China's latest patents, Technical Efficacy Thesaurus, Application Domain, Technology Topic, Popular Technical Reports.
© 2024 PatSnap. All rights reserved.Legal|Privacy policy|Modern Slavery Act Transparency Statement|Sitemap|About US| Contact US: help@patsnap.com