Processing mold used for carbon fiber complex core pressing moulding
A technology of pressing and processing molds, which is applied in the direction of cable/conductor manufacturing, electrical components, circuits, etc., and can solve the problems of uneven thermal curing and thermal melting of fiber-resin bonded composite materials, large thermal expansion coefficients of metal molds, and consistent materials Poor performance and other problems, to achieve the effect of small molding error, good consistency, and reduce thermal stress
- Summary
- Abstract
- Description
- Claims
- Application Information
AI Technical Summary
Problems solved by technology
Method used
Image
Examples
Embodiment Construction
[0013] See figure 1 , figure 2 , image 3 , Figure 4 and Figure 5 As shown, a processing mold for compression molding of a carbon fiber composite core includes a horizontally arranged mold 2, and an infrared generator 3 is arranged on the outer surface of the mold 2, and the infrared generator 3 is formed by winding a resistance wire around the outer surface of the mold 2 , the carbon fiber composite core runs through the through hole of the mold 2 .
[0014] Wherein, the through holes of the mold 2 can be set in circular, square, special-shaped, plate-shaped and other shapes according to the shape requirements of the carbon fiber composite core.
[0015] Wherein, the mold 2 is made of quartz or ceramic material.
[0016] Among them, the infrared generator 3 generates medium and short-wave infrared rays (1 μm ~ 4 μm) through the resistance wire to penetrate quartz or ceramic materials to generate thermal effects.
[0017] Wherein, on the six faces of the carbon fiber ...
PUM
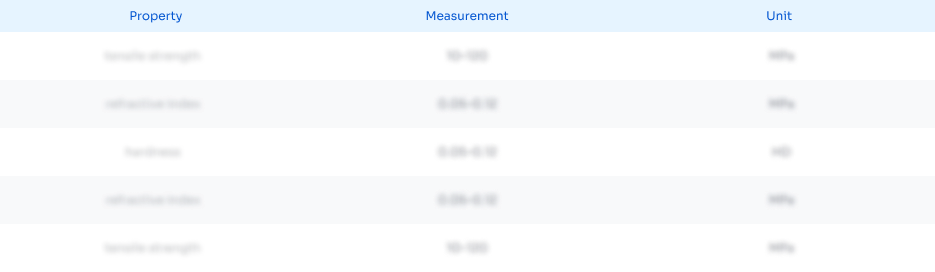
Abstract
Description
Claims
Application Information

- Generate Ideas
- Intellectual Property
- Life Sciences
- Materials
- Tech Scout
- Unparalleled Data Quality
- Higher Quality Content
- 60% Fewer Hallucinations
Browse by: Latest US Patents, China's latest patents, Technical Efficacy Thesaurus, Application Domain, Technology Topic, Popular Technical Reports.
© 2025 PatSnap. All rights reserved.Legal|Privacy policy|Modern Slavery Act Transparency Statement|Sitemap|About US| Contact US: help@patsnap.com