Rolling oil and preparation process thereof
A technology of rolling oil and reactor, which is applied in the field of rolling oil, can solve the problems that the waste liquid cannot meet the three wastes treatment discharge standards, the surface of the steel plate cannot reach the smoothness, and affect the physical and mental health of workers, so as to ensure the smoothness and reduce the Effect of friction and reduction of rolling load
- Summary
- Abstract
- Description
- Claims
- Application Information
AI Technical Summary
Problems solved by technology
Method used
Examples
Embodiment 1
[0019] first step
[0020] First, 550 kilograms of water, 95 kilograms of sodium molybdate and 55 kilograms of sodium thiosulfate are directly added to the first reaction kettle, fully stirred for 30 minutes;
[0021] second step
[0022] The phosphoric acid of 115 kilograms and the triethanolamine of 55 kilograms are joined in the second reactor and directly joined in the first reactor after reacting for 35 minutes;
[0023] third step
[0024] Add 55 kg of triethanolamine and lubricant stearic acid into the third reaction kettle and heat to 70-75°C, and pour it into the first reaction kettle after reacting for 60 minutes;
[0025] the fourth step
[0026] Add 22 kg of emulsifier castor oil polyoxyethylene ether, 30 kg of Ninar and 6 kg of regulator sodium hydroxide to the first reaction kettle and stir for 55 minutes to obtain milky white-milk Yellow viscous liquid rolling oil.
Embodiment 2
[0028] first step
[0029] First directly add 600 kilograms of water, 85 kilograms of ammonium molybdate and 60 kilograms of sodium thiosulfate into the first reaction kettle, fully stir for 35 minutes;
[0030] second step
[0031] The phosphoric acid of 120 kilograms and the triethanolamine of 50 kilograms are joined in the second reactor and directly join in the first reactor after reacting for 40 minutes;
[0032] third step
[0033] Add 50 kg of triethanolamine and lubricant stearic acid into the third reaction kettle and heat to 70-75°C, and pour into the first reaction kettle after reacting for 55 minutes;
[0034] the fourth step
[0035] Add 24 kg of emulsifier Pingping O-20, 25 catties of Ninar and 6.5 kg of regulator sodium hydroxide to the first reaction kettle and stir for 70 minutes to produce milky white-milky yellow viscous liquid rolling oil.
Embodiment 3
[0037] first step
[0038] First, 500 kilograms of water, 80 kilograms of trisodium phosphate and 50 kilograms of sodium thiosulfate are directly added to the first reaction kettle, fully stirred for 40 minutes;
[0039] second step
[0040] The phosphoric acid of 110 kilograms and the triethanolamine of 53 kilograms are joined in the second reactor and directly joined in the first reactor after reacting for 30 minutes;
[0041] third step
[0042] Add 53 kg of triethanolamine and lubricant stearic acid into the third reaction kettle and heat to 70-75°C, and pour it into the first reaction kettle after reacting for 70 minutes;
[0043] the fourth step
[0044] Add 20 kg of emulsifier OP10, 35 kg of Ninar and 6.1 kg of regulator potassium hydroxide to the first reaction kettle and stir for 50 minutes to obtain milky white-milky yellow sticky Liquid rolling oil.
PUM
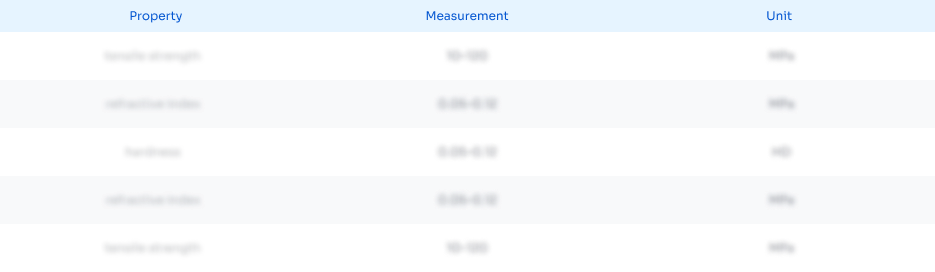
Abstract
Description
Claims
Application Information

- R&D
- Intellectual Property
- Life Sciences
- Materials
- Tech Scout
- Unparalleled Data Quality
- Higher Quality Content
- 60% Fewer Hallucinations
Browse by: Latest US Patents, China's latest patents, Technical Efficacy Thesaurus, Application Domain, Technology Topic, Popular Technical Reports.
© 2025 PatSnap. All rights reserved.Legal|Privacy policy|Modern Slavery Act Transparency Statement|Sitemap|About US| Contact US: help@patsnap.com