Temperature compensation method for composite material workpiece autoclave forming workpiece
A technology of autoclave forming and temperature compensation, which is applied in the field of composite material autoclave forming, can solve the problems of reduced production efficiency, low heating rate of parts, and increased production costs, so as to improve the quality of part forming and increase production efficiency , the effect of reducing production costs
- Summary
- Abstract
- Description
- Claims
- Application Information
AI Technical Summary
Problems solved by technology
Method used
Image
Examples
Embodiment Construction
[0032] The technical solutions of the present invention will be described in detail below in conjunction with the accompanying drawings.
[0033] The invention provides a method for compensating the temperature of an autoclave molded part of a composite material part, which mainly uses a heater to heat the lower temperature position of the part to realize temperature compensation.
[0034] Cooperate figure 1 Shown, be the concrete realization process of the present invention, step is:
[0035] (1) Simplify the autoclave model according to the structure and operating principle of the autoclave, and then define the air density, viscosity, thermal conductivity, pressure, and wind speed in the autoclave according to the curing process; the density and specific heat capacity of the tooling and parts , thermal conductivity and the heat release rate function of the solidification of the part, the temperature field is calculated through the temperature field simulation software, and ...
PUM
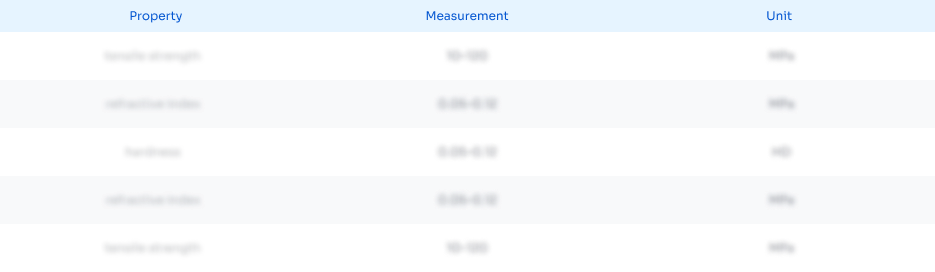
Abstract
Description
Claims
Application Information

- R&D
- Intellectual Property
- Life Sciences
- Materials
- Tech Scout
- Unparalleled Data Quality
- Higher Quality Content
- 60% Fewer Hallucinations
Browse by: Latest US Patents, China's latest patents, Technical Efficacy Thesaurus, Application Domain, Technology Topic, Popular Technical Reports.
© 2025 PatSnap. All rights reserved.Legal|Privacy policy|Modern Slavery Act Transparency Statement|Sitemap|About US| Contact US: help@patsnap.com