Antistatic nylon material and preparation method thereof
An antistatic and antistatic agent technology, which is applied in the field of antistatic nylon materials and their preparation, can solve the problems that the material cannot maintain the antistatic effect for a long time, and the material turns back to the insulating effect, and achieves obvious antistatic effect and antistatic effect. The effect is stable and the effect of reducing the surface resistivity
- Summary
- Abstract
- Description
- Claims
- Application Information
AI Technical Summary
Problems solved by technology
Method used
Image
Examples
Embodiment 1
[0039] Take polyamide (PA6) 78.5% by weight percentage, antistatic agent (carbon fiber) 20.2%, antioxidant 1010 and 168 are 0.2%, lubricant TAF and siloxane are 0.3%, nucleating agent CAV102 0.3% %. Preparation of PA6 modified antistatic material.
[0040] Composite materials were prepared by the following methods:
[0041] a. Weighing raw materials, including polyamide (100° C. for 4 h), and drying said raw materials;
[0042] b. Add the dried polyamide to the high-speed mixer, add lubricant, nucleating agent and antioxidant, and mix at high speed for about 4 minutes;
[0043] c. Put the fully mixed and dried raw materials and additives into a twin-screw extruder, add 20.2% carbon fiber to carry out reinforcement filling extrusion granulation, and obtain a modified antistatic polyamide material.
[0044] The temperature setting of each section of the twin-screw extruder is: the temperature of the first zone is 100°C, the temperature of the second zone is 220°C, the temperatu...
Embodiment 2
[0046] Weigh polyamide (PA6) 72.7% by weight percentage, antistatic agent (MH2030) 26%, antioxidant 1010 and 168 are 0.2%, lubricant TAF and siloxane are 0.3%, nucleating agent CAV102 0.3 %. Preparation of PA6 modified antistatic material.
[0047] Composite materials were prepared by the following methods:
[0048] a. Weigh raw materials, including polyamide PA6 (100°C for 4h), antistatic agent MH2030 (80°C for 4h), and dry the raw materials respectively;
[0049] b. Add the dried polyamide and antistatic agent to the high-speed mixer, and add lubricant, nucleating agent and antioxidant, and mix at high speed for about 4 minutes;
[0050] c. Put the fully mixed and dried raw materials and additives into a twin-screw extruder for direct granulation to prepare a modified antistatic polyamide material.
[0051] The temperature setting of each section of the twin-screw extruder is: the temperature of the first zone is 100°C, the temperature of the second zone is 230°C, the tem...
Embodiment 3
[0053] Weigh polyamide (PA6) 78.5% by weight percentage, antistatic agent (CM6-25) 20.2%, antioxidant 1010 and 168 are 0.2%, lubricant TAF and siloxane are 0.3%, nucleating agent CAV102 0.3%. Preparation of PA6 modified antistatic material.
[0054] Composite materials were prepared by the following methods:
[0055] a. Weigh raw materials, including polyamide PA6 (100°C 4h), antistatic agent CM6-25 (90°C 4h), and dry the raw materials respectively;
[0056] b. Add the dried polyamide and antistatic agent to the high-speed mixer, and add lubricant, nucleating agent and antioxidant, and mix at high speed for about 4 minutes;
[0057] c. Put the fully mixed and dried raw materials and additives into a twin-screw extruder for direct granulation to prepare a modified antistatic polyamide material.
[0058] The temperature setting of each section of the twin-screw extruder is: the temperature of the first zone is 90°C, the temperature of the second zone is 200°C, the temperature...
PUM
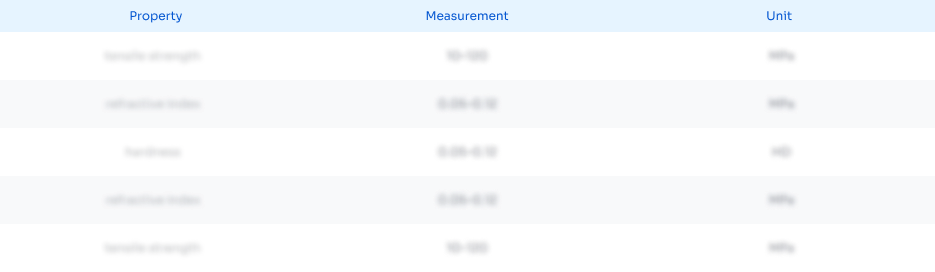
Abstract
Description
Claims
Application Information

- R&D Engineer
- R&D Manager
- IP Professional
- Industry Leading Data Capabilities
- Powerful AI technology
- Patent DNA Extraction
Browse by: Latest US Patents, China's latest patents, Technical Efficacy Thesaurus, Application Domain, Technology Topic, Popular Technical Reports.
© 2024 PatSnap. All rights reserved.Legal|Privacy policy|Modern Slavery Act Transparency Statement|Sitemap|About US| Contact US: help@patsnap.com