Three-drum forming method of full steel wire loading radial tire via one-time method
A molding method and radial tire technology, applied in the field of tire manufacturing, to achieve the effects of improving automation, optimizing tire storage space and transportation channels, and reducing labor intensity
- Summary
- Abstract
- Description
- Claims
- Application Information
AI Technical Summary
Problems solved by technology
Method used
Image
Examples
Embodiment Construction
[0032] Carcass tube fitting:
[0033] The operator installs the left and right bead on the left bead presetting frame 7 and the right bead presetting frame 8 on both sides of the carcass tube fitting drum 9, on the left and right bead rods 5 and 6 → the sidewall and the The inner liner composite parts are automatically compounded in the machine → the carcass tube bonding drum 9 is opened to the bonding diameter, and the circumference is fixed at the position of the compound part → the operator will cut the compound part in advance to the length and wait on the feeding belt The end is led to the fan-shaped drum plate of the carcass tube fitting drum 9, and the drum plate vacuum sucks the end → the carcass tube fitting drum 9 rotates one circle to the joint position of the inner liner → start the inner liner and sidewall composite parts Automatic rolling device, the inner lining layer sewing wheel 26 automatically presses the joint between the sidewall and the inner lining layer...
PUM
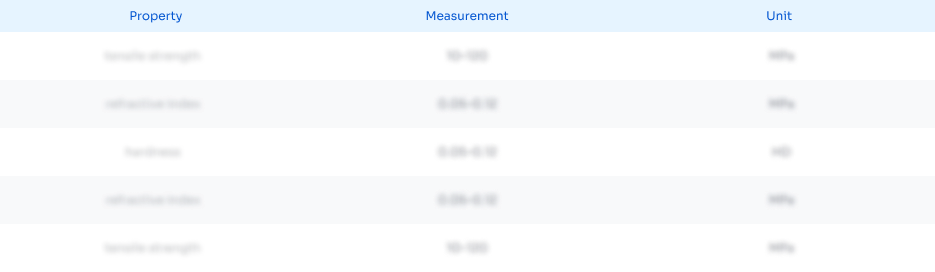
Abstract
Description
Claims
Application Information

- R&D
- Intellectual Property
- Life Sciences
- Materials
- Tech Scout
- Unparalleled Data Quality
- Higher Quality Content
- 60% Fewer Hallucinations
Browse by: Latest US Patents, China's latest patents, Technical Efficacy Thesaurus, Application Domain, Technology Topic, Popular Technical Reports.
© 2025 PatSnap. All rights reserved.Legal|Privacy policy|Modern Slavery Act Transparency Statement|Sitemap|About US| Contact US: help@patsnap.com