Process for manufacturing septic tank by using glass fibre reinforced plastic
A technology of glass fiber and reinforced plastics, which is applied in the field of septic tanks made of glass fiber reinforced plastics and composite molded septic tanks. In spite of the high cost, it achieves the effect of good appearance quality, strong designability, and reasonable and advanced pipe wall structure
- Summary
- Abstract
- Description
- Claims
- Application Information
AI Technical Summary
Problems solved by technology
Method used
Examples
Embodiment 1
[0017] 1. Weigh 42% of unsaturated polyester resin (196DC), 1% of curing agent, 1% of accelerator, 7% of glass cloth, 7% of chopped strand mat (EMC450-1270), 4% of surface mat, net Gauze 3% (JG149-2003 standard 2%; JG158-2004 standard 1%), glass fiber direct roving 23%, glass spray yarn 12%, unsaturated polyester resin, curing agent, accelerator in the above substances Heat, melt, mix and stir until it becomes a paste resin mixture;
[0018] 2. Take the septic tank mold, place its mouth downward on the shelf, wax the outside of the mold and make a lining, paste the glass fiber cloth, take the above paste resin mixture and spread it evenly on the outside of the waterproof cloth layer by layer , and paste a layer of glass fiber cloth on the surface of each layer of smearing, the thickness of each layer of smearing layer is 4cm, smearing 3 layers, the first layer is winding in the shape of rice, the second layer is winding at 45° of the pipe, and the third layer is winding 135° ...
Embodiment 2
[0022] 1. Weigh 42% of unsaturated polyester resin (196DC), 0.7% of curing agent, 0.7% of accelerator, 7% of glass cloth, 7.3% of chopped strand mat (EMC450-1270), 4.3% of surface mat, net Gauze 3% (JG149-2003 standard 2%; JG158-2004 standard 1%), glass fiber direct roving 23%, glass spray yarn 12%, unsaturated polyester resin, curing agent, accelerator in the above substances Heat, melt, mix and stir until it becomes a paste resin mixture;
[0023] 2. Take the septic tank mold, place the mouth down on the shelf, wax and line the outside of the mold, paste the glass fiber cloth, take the above paste dry mixture and put it on the waterproof cloth layer by layer Apply evenly, and paste a layer of glass fiber cloth on the surface of each layer. The thickness of each layer is 3cm. Apply 3 layers. The layer is 135°winding of the pipe;
[0024] 3. After the paste is solidified, demould from the opening side of the mold; wax the upper mold on the mold made of glass fiber cloth and ...
PUM
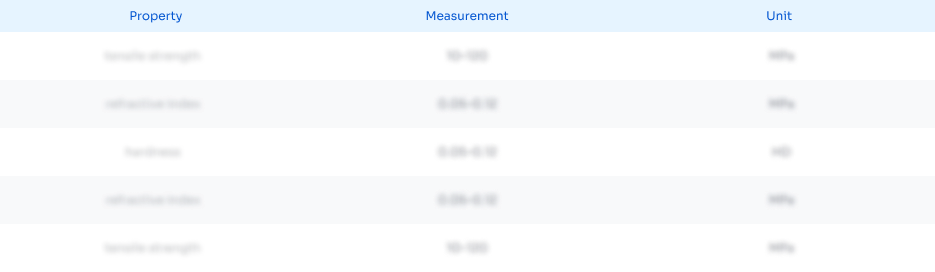
Abstract
Description
Claims
Application Information

- R&D
- Intellectual Property
- Life Sciences
- Materials
- Tech Scout
- Unparalleled Data Quality
- Higher Quality Content
- 60% Fewer Hallucinations
Browse by: Latest US Patents, China's latest patents, Technical Efficacy Thesaurus, Application Domain, Technology Topic, Popular Technical Reports.
© 2025 PatSnap. All rights reserved.Legal|Privacy policy|Modern Slavery Act Transparency Statement|Sitemap|About US| Contact US: help@patsnap.com